工場ピッキング作業の効率化とコツ:工場におけるピッキングミス削減
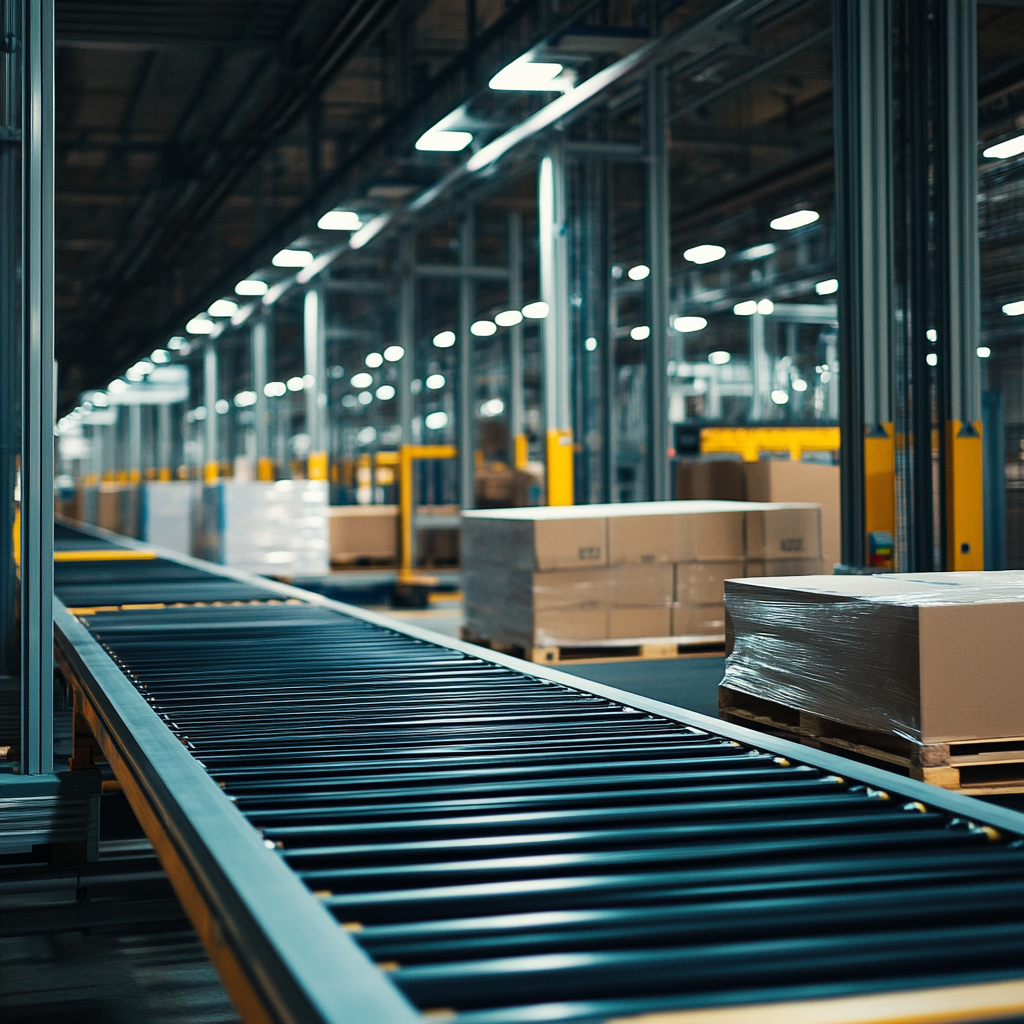
工場でのピッキング作業は、正確さとスピードが求められる一方で、未経験者でも活躍できるチャンスが多い仕事です。この記事では、ピッキング作業の基本から、効率を上げるためのコツ、そして未経験者がスムーズに業務に取り組むためのポイントを解説します。
ピッキング作業の基本と種類
ピッキングとは?作業の全体像
ピッキング作業は、指定された商品や部品を倉庫や工場内から集める作業です。
この工程は、製品を顧客に届ける上で非常に重要な役割を果たします。
ここでは、ピッキング作業の基本的な流れと注意点を解説します。
ピッキング作業は、単に商品を集めるだけでなく、その後の梱包や出荷に繋がる重要なプロセスです。正確かつ迅速なピッキングは、顧客満足度向上に直結します。
製造業においては、必要な部品を必要な時に供給することで、生産ラインの効率的な運用を支えます。
また、物流業界においては、多種多様な商品を効率的に集めることで、迅速な配送を実現する上で欠かせない工程です。
ピッキング作業の精度とスピードは、企業全体のサプライチェーンの効率に大きく影響を与えるため、その重要性は非常に高いといえます。
ピッキング作業の効率化は、コスト削減にも大きく貢献します。作業時間の短縮やミスの削減は、人件費や返品コストの削減に繋がり、企業全体の利益向上に貢献します。
近年では、自動化技術の導入も進んでおり、ピッキングロボットや自動搬送システムなどが活用されるケースも増えています。これにより、作業員の負担を軽減しつつ、より効率的なピッキングが可能になっています。
ピッキング作業は、その種類や方法、使用する機器によって、作業効率や精度が大きく左右されます。そのため、ピッキング作業を行う際には、それぞれの特性を理解し、最適な方法を選択することが重要です。また、作業員は、常に安全を意識し、正確な作業を心がける必要があります。
シングルピッキングとトータルピッキング
ピッキングには主に、シングルピッキング(摘み取り方式)とトータルピッキング(種まき方式)の2種類があります。
それぞれの特徴と、どのような場合に適しているのかを解説します。
シングルピッキングは、注文ごとに商品をピッキングする方法です。
一方、トータルピッキングは、複数の注文の商品をまとめてピッキングし、後で注文ごとに仕分ける方法です。
シングルピッキングは、少量多品種のピッキングに適しており、主にECサイトなどの小規模な注文処理に適しています。この方式では、ピッキングリストに従って、一つ一つの注文に対して商品を集めるため、正確性が高く、誤出荷のリスクを低減できます。
一方、トータルピッキングは、大量の注文を効率的に処理するのに適しています。主に、スーパーマーケットや大規模な物流センターなどで採用されています。この方式では、最初に全ての商品をピッキングし、その後に注文ごとに仕分けるため、ピッキング作業の効率を大幅に向上させることができます。
シングルピッキングでは、ピッキング作業者が複数の商品を同時に扱うことが少ないため、作業ミスが比較的少ないという利点があります。また、ピッキングした商品をすぐに梱包できるため、出荷までのリードタイムを短縮できます。
トータルピッキングでは、一度に複数の商品をピッキングするため、作業者の移動距離を短縮できます。しかし、ピッキング後の仕分け作業が必要となるため、仕分け作業の正確性が重要になります。
それぞれのピッキング方式は、扱う商品の種類や量、注文の頻度などによって最適なものが異なります。そのため、それぞれの現場の状況に合わせて、最適なピッキング方式を選択することが、効率的な作業を実現するための鍵となります。
その他のピッキング方式
ウェーブピッキングやマルチピッキングなど、より効率的なピッキング方式も存在します。
これらの方式がどのように作業効率を向上させるのかを解説します。
ウェーブピッキングは、時間帯や配送ルートごとにまとめてピッキングを行う方式です。
マルチピッキングは、複数人で同時に複数の商品をピッキングする方法です。
これらの方式を導入することで、作業時間の短縮や、より効率的な作業が可能になります。
ウェーブピッキングは、特に配送ルートが決まっている場合に有効です。時間帯や配送ルートごとにピッキングをまとめることで、ピッキング後の仕分け作業を効率化し、配送までのリードタイムを短縮できます。例えば、午前中に配送する商品と午後に配送する商品を分けてピッキングすることで、配送トラックへの積み込み作業がスムーズに行えます。
マルチピッキングは、複数人で同時に作業を行うため、全体の作業時間を大幅に短縮できます。大規模な倉庫や工場で、複数のピッキング作業者が同時に作業を行うことで、短時間で大量の商品をピッキングできます。
さらに、ゾーンピッキングという方式もあります。これは、倉庫をいくつかのゾーンに分け、担当者を決めてピッキングを行う方法です。これにより、作業者は自分の担当ゾーンに集中してピッキングできるため、効率性と正確性を向上させることができます。
また、デジタルピッキングシステムという、表示器やランプを使ってピッキング場所を指示するシステムもあります。これは、作業者がピッキング場所を迷うことなく、迅速に作業できるため、ピッキング効率を大幅に向上させます。
近年では、AIやロボットを活用したピッキングシステムも登場しています。これらのシステムは、ピッキング作業を自動化することで、人手不足の解消や、作業効率の大幅な向上に貢献しています。
それぞれのピッキング方式には、異なるメリットとデメリットがあるため、自社の状況に合わせて最適な方式を選択することが重要です。
ピッキング作業の効率化
作業前の準備と確認
ピッキングリストの確認、倉庫内のレイアウト把握、使用する機材の準備など、作業前の準備をしっかりと行うことで、作業効率を大幅に向上させることができます。
ピッキングリストの内容をよく確認し、商品の場所や数量を把握します。
また、倉庫内のレイアウトを把握し、効率的な移動ルートを計画します。
必要な機材(ハンディターミナル、カートなど)を準備し、すぐに使える状態にしておくことが重要です。
作業前の準備は、ピッキング作業の効率と精度を左右する非常に重要な要素です。
ピッキングリストは、単なる指示書ではなく、ピッキング作業の設計図と考えるべきです。商品の品名、品番、数量、保管場所などの情報を正確に把握することで、作業中の迷いやミスを減らすことができます。
倉庫内のレイアウトを把握することは、移動時間を短縮し、作業効率を高めるために不可欠です。商品の配置を把握し、最短距離でピッキングできるように、移動ルートを事前に計画することが重要です。また、倉庫内には、通路や棚など、移動を妨げるものがあるため、これらを考慮して最適なルートを選択する必要があります。
使用する機材は、作業効率を上げるための重要なツールです。ハンディターミナルは、商品のバーコードを読み取ることで、商品の情報を確認したり、ピッキング状況を記録したりできます。また、カートや台車は、商品を運搬する際に、作業員の負担を軽減します。これらの機材を事前に準備しておくことで、作業をスムーズに進めることができます。
さらに、作業前に、ピッキングリストと実際の商品を照合することで、ピッキングミスを未然に防ぐことができます。特に、似たような商品がある場合や、ピッキングリストの記載に誤りがある場合には、この確認作業が非常に重要になります。
作業前の準備をしっかりと行うことで、ピッキング作業の効率と精度を向上させ、よりスムーズな作業を実現することができます。また、作業時間の短縮やミスの削減にもつながり、結果として、作業員全体の負担軽減やコスト削減にも貢献することができます。
ピッキング時のコツ
最短ルートでの移動、商品の正確な確認、作業しやすい服装など、ピッキング作業を効率的に進めるためのコツを具体的に解説します。
倉庫内を移動する際は、最短ルートを意識することで、移動時間を短縮できます。
商品をピッキングする際には、商品名や数量をしっかりと確認し、ミスを防ぐことが重要です。
また、動きやすい服装で作業することで、作業効率が向上します。
必要に応じて、滑りにくい手袋や安全靴を着用しましょう。
ピッキング作業は、正確性とスピードが求められるため、効率的な作業方法を身につけることが重要です。まず、倉庫内を移動する際は、最短ルートを意識することが大切です。倉庫のレイアウトを把握し、ピッキングリストに基づいて、最も効率的な移動経路を計画しましょう。
商品をピッキングする際には、商品名や数量をしっかりと確認しましょう。商品の取り間違いや数量不足は、その後の作業に大きな影響を与えるため、確認作業は怠らないようにしましょう。ハンディターミナルを使用する場合は、画面表示と実際の商品を照合し、バーコードを正確に読み取ることも重要です。
作業時の服装も、作業効率に影響を与えます。動きやすい服装を着用し、作業の妨げになるようなものは身につけないようにしましょう。また、安全靴や滑りにくい手袋など、作業内容に応じて適切な保護具を着用することも重要です。
ピッキング作業中は、常に周囲の状況に注意しましょう。他の作業員やフォークリフトなどの動きに注意し、事故を未然に防ぐように心がけましょう。特に、狭い場所や見通しの悪い場所では、注意が必要です。
また、作業中に疑問点や不明な点があった場合は、すぐに先輩社員や管理者に確認しましょう。曖昧なまま作業を進めると、ミスにつながる可能性があります。
さらに、ピッキング作業を効率的に行うためには、作業スペースを整理整頓することも重要です。作業スペースが散らかっていると、商品を探すのに時間がかかったり、足元が危険になることがあります。
これらのコツを実践することで、ピッキング作業をより効率的に、そして安全に進めることができます。
ハンディターミナル活用
ハンディターミナルを効果的に活用することで、ピッキングミスを減らし、作業時間の短縮が可能です。
正しい使い方と、そのメリットを説明します。
ハンディターミナルは、商品のバーコードを読み取ることで、ピッキング情報を確認できます。
これにより、商品の取り間違いを防ぐことができ、ピッキング作業の効率化につながります。
また、ハンディターミナルには、ピッキングする商品の場所や数量が表示されるため、作業者は迷うことなくピッキングを行うことができます。
さらに、ピッキング状況のデータ管理にも活用できるため、在庫管理の効率化にも貢献します。
ハンディターミナルは、現代のピッキング作業において不可欠なツールです。
その機能を最大限に活用することで、作業効率を大幅に向上させることができます。ハンディターミナルは、商品のバーコードを読み取ることで、商品名、品番、数量、保管場所などの情報を瞬時に表示できます。
この機能により、作業者は、ピッキングリストを見ながら商品を探す手間を省き、スムーズに作業を進めることができます。
また、ハンディターミナルには、ピッキングした商品の情報を記録する機能もあります。これにより、ピッキング状況をリアルタイムで把握できるため、在庫管理の正確性を高めることができます。さらに、ピッキング作業の履歴をデータとして保存できるため、作業状況の分析や改善にも役立ちます。
ハンディターミナルを使用する際には、正しい使い方を学ぶことが重要です。まず、ハンディターミナルの電源を入れ、必要な情報を入力します。次に、ピッキングする商品のバーコードを読み取り、画面に表示される情報を確認します。もし、商品が間違っていた場合は、エラーが表示されるため、すぐに修正できます。ピッキングが完了したら、その情報をハンディターミナルに入力し、次の作業に移ります。
ハンディターミナルの操作に慣れるまでは、時間がかかるかもしれませんが、繰り返し使用することで、スムーズに操作できるようになります。
また、ハンディターミナルは、常に清潔に保ち、充電切れに注意する必要があります。ハンディターミナルが故障すると、作業に支障が出るため、定期的なメンテナンスを行うことも重要です。
ハンディターミナルを効果的に活用することで、ピッキング作業の効率性と精度を向上させ、よりスムーズな作業を実現できます。
未経験者が活躍するためのポイント
未経験でも安心!基礎知識
ピッキング作業は、未経験者でもすぐに始められる仕事です。
基本的な作業内容や注意点、安全に作業を進めるための知識を解説します。
ピッキング作業は、指示書に基づいて、倉庫内から商品を集める作業です。
この作業は比較的単純で、特別な資格や経験は必要ありません。
しかし、安全に作業を進めるためには、基本的な知識を身につけておく必要があります。
例えば、商品の持ち方や、運搬時の注意点などを理解することが重要です。
ピッキング作業は、一見すると単純な作業に見えますが、正確性と効率性が求められる仕事です。
未経験者でも、基本的な知識と注意点を理解すれば、十分に活躍することができます。まず、ピッキング作業の基本は、ピッキングリストやハンディターミナルの指示に従って、商品を集めることです。ピッキングリストには、商品の品名、品番、数量、保管場所などの情報が記載されています。これらの情報を正確に読み取り、商品をピッキングすることが重要です。
商品をピッキングする際には、安全に注意することが大切です。重い商品を運ぶ際には、腰を痛めないように、正しい姿勢で持ち上げる必要があります。また、高い場所にある商品をピッキングする際には、足元に注意し、安定した場所で作業を行うようにしましょう。もし、危険を感じた場合は、無理せずに他の人に手伝ってもらうようにしましょう。
倉庫内は、様々な種類のフォークリフトや運搬車が行き来しているため、常に周囲の状況に注意する必要があります。特に、フォークリフトの近くを歩く際には、十分に注意し、事故を防ぐように心がけましょう。
また、ピッキング作業中は、常に清潔な状態を保つことも重要です。汚れた手で商品を触ると、商品が汚れてしまうだけでなく、衛生面にも悪影響を及ぼします。作業前に手を洗い、必要に応じて手袋を着用するようにしましょう。
さらに、ピッキング作業中に、不明な点や疑問点があった場合は、すぐに先輩社員や管理者に確認しましょう。自己判断で作業を進めると、ミスにつながる可能性があります。未経験者向けの研修や教育制度を活用し、ピッキング作業の基本をしっかりと学ぶことが、安全で効率的な作業を実現するために重要です。
研修と教育体制について
多くの工場や倉庫では、未経験者向けの研修や教育制度が整っています。
どのように業務を学ぶことができるのか、具体的な内容を紹介します。
入社時には、ピッキング作業の基本や、倉庫内のルールについて研修が行われます。
また、先輩社員がマンツーマンで指導を行うなど、教育体制も整っています。
研修では、ハンディターミナルの使い方や、ピッキングリストの見方などを学ぶことができます。
さらに、安全に作業するための知識や、緊急時の対応についても学ぶことができます。
ピッキング作業は、未経験者でも始めやすい仕事ですが、安全かつ効率的に作業を行うためには、きちんとした研修と教育が不可欠です。
多くの工場や倉庫では、未経験者向けの研修制度を設けており、入社時にピッキング作業の基本的な知識やスキルを学ぶことができます。
研修では、ピッキング作業の基本的な流れや、ピッキングリストの見方、ハンディターミナルの使い方などを学びます。また、倉庫内のルールや安全に関する注意事項についても説明があります。
さらに、先輩社員がマンツーマンで指導するOJT(On-the-JobTraining)形式の教育制度も導入されています。OJTでは、実際の作業を通じて、より実践的なスキルを身につけることができます。先輩社員は、未経験者の疑問や不安に丁寧に答え、安心して作業に取り組めるようにサポートします。
また、定期的な研修や勉強会なども実施されている場合があります。これらの研修では、ピッキング作業の効率化や、最新のピッキングシステムについて学ぶことができます。さらに、安全に関する知識を再確認し、事故防止に努めることができます。
研修や教育制度は、未経験者がピッキング作業に慣れるまでのサポートだけでなく、スキルアップのための機会も提供しています。これらの制度を活用することで、未経験者でも、安心してピッキング作業に取り組むことができるだけでなく、プロフェッショナルとして成長することも可能です。
企業によっては、資格取得を支援する制度もあります。ピッキング作業に関連する資格を取得することで、より高いレベルでの作業が可能になります。未経験者でも、研修や教育制度を積極的に活用し、スキルアップを目指すことが大切です。
ピッキング注意点
注意すべき点
作業中のケガやミスを防ぐため、注意すべきポイントや、負担を軽減するための工夫について解説します。
ピッキング作業中は、周囲の状況をよく確認し、他の作業者やフォークリフトなどに注意する必要があります。
また、重い商品を運ぶ際には、腰を痛めないように注意し、無理のない範囲で作業を行うことが重要です。
商品の落下によるケガを防ぐため、高い場所に商品を積み上げすぎないように注意しましょう。
ハンディターミナルの画面をしっかり確認し、商品の取り間違いがないように注意することも大切です。
作業に集中しすぎると、体調が悪くなることもあるので、適度に休憩を挟みながら作業を進めましょう。
ピッキング作業は、安全に注意して行うことが重要です。倉庫内には、フォークリフトや他の作業員が動いているため、常に周囲の状況をよく確認し、事故を防ぐように心がけましょう。
特に、フォークリフトは、急に方向転換したり、停止したりすることがあるため、十分に注意する必要があります。
また、重い商品を運ぶ際には、腰を痛めないように、正しい姿勢で持ち上げるようにしましょう。無理な体勢で持ち上げたり、重すぎる物を運んだりすると、腰を痛める原因になります。
高い場所にある商品をピッキングする際には、落下によるケガを防ぐため、十分に注意が必要です。不安定な足場で作業したり、商品を積み上げすぎたりしないようにしましょう。もし、危険を感じた場合は、無理せずに他の人に手伝ってもらうようにしましょう。
ハンディターミナルの画面をしっかり確認し、商品の取り間違いがないように注意することも大切です。焦って作業をすると、商品の取り間違いが発生しやすくなります。一つ一つの商品を丁寧に確認するようにしましょう。
ピッキング作業に集中しすぎると、体調が悪くなることもあるので、適度に休憩を挟みながら作業を進めるようにしましょう。水分補給を忘れず、体調に異変を感じたら、無理せずに休憩を取るようにしましょう。
また、ピッキング作業は、長時間同じ姿勢で作業することが多いため、疲労がたまりやすいです。作業中にストレッチや軽い運動を取り入れるなどして、疲労を軽減するように努めましょう。
さらに、作業環境を整えることも重要です。倉庫内は、温度や湿度が変化しやすい場所であるため、適切な服装で作業するようにしましょう。また、照明が暗い場合は、十分な明るさを確保するようにしましょう。
これらの注意点を守ることで、ピッキング作業中のケガやミスを未然に防ぎ、安全に作業を行うことができます。
ピッキングミスが多発する主な原因
作業ルール不徹底と人為的ミス
作業者によってピッキング方法が異なると、ミスが発生しやすくなります。
また、作業ルールが曖昧な場合や徹底されていない場合も、ピッキングミスが頻発する原因となります。
正確な指示の読解不足や、空間把握能力の欠如も、人為的ミスの要因です。
作業者個人の経験や勘に頼ったピッキングは、どうしてもミスが発生するリスクを高めます。特に、新規作業者や経験の浅い作業者は、作業ルールを十分に理解していないため、ミスを起こしやすい傾向があります。さらに、繁忙期などで作業者の集中力が低下すると、単純なミスが発生しやすくなるでしょう。
例えば、指示書に記載された棚番号を誤って認識したり、似たような商品を間違えてピッキングしたりするケースが考えられます。
また、作業中に他の作業者とコミュニケーションを取る際に、注意散漫になり、ミスにつながることもあります。
これらの人為的なミスは、作業環境やルールを改善することで、ある程度は防ぐことができます。
作業ルールの明確化、作業手順の標準化、そして作業者の教育と訓練が重要です。
さらに、作業者の疲労を軽減するための休憩時間の確保や、作業環境の改善も有効です。
これらの対策を講じることで、人為的なミスを減らし、ピッキングの精度を向上させることができます。
不適切なロケーションと作業環境
ロケーション管理が最適化されていない場合、ピッキング作業の効率が低下し、ミスも発生しやすくなります。
また、作業環境が整理整頓されていないと、ポカミスを誘発する可能性があります。
具体的には、商品が整理されずに乱雑に保管されている場合、目的の商品を見つけ出すのに時間がかかり、ピッキングミスが発生しやすくなります。例えば、棚の奥に商品が隠れてしまっていたり、異なる商品が同じ場所に置かれていたりすると、作業者は誤った商品をピッキングする可能性が高まります。
また、棚の配置が作業動線を考慮していない場合も、ピッキング作業の効率を低下させる要因となります。
例えば、ピッキングする商品が離れた場所に配置されていると、作業者は移動に時間を費やし、疲労が蓄積します。その結果、集中力が低下し、ミスを引き起こす可能性が高まります。さらに、通路が狭く、作業者がスムーズに移動できない場合も、ピッキング作業の効率を低下させ、ミスを誘発する原因となります。
作業環境の整理整頓も非常に重要です。
床に物が散乱していると、作業者がつまずいて怪我をするリスクがあるだけでなく、作業効率も低下します。
また、作業スペースが狭い場合、作業者は窮屈な姿勢でピッキング作業を行わなければならず、ミスを起こしやすくなります。
これらの問題を解決するためには、ロケーション管理の最適化と作業環境の整理整頓が不可欠です。
棚の配置を見直したり、商品の保管場所を明確にしたりすることで、ピッキング作業の効率を向上させ、ミスを減らすことができます。さらに、作業スペースを十分に確保し、作業者が快適に作業できる環境を整備することが重要です。
情報共有の不足とダブルチェックの不備
必要な情報が作業者間で共有されていない場合、誤ったピッキングにつながる可能性があります。
ダブルチェックが適切に行われていない場合も、ミスを見逃す原因となります。
例えば、ピッキングリストに記載された情報が古かったり、誤っていたりする場合、作業者は正しい商品をピッキングすることができません。また、ピッキングリストの読解が難しい場合も、誤ったピッキングにつながる可能性があります。
さらに、作業者間で情報が共有されていないと、ピッキング作業の重複や抜けが発生する可能性もあります。
例えば、ある作業者がすでにピッキングを終えた商品を、別の作業者が再度ピッキングしてしまうケースが考えられます。また、ピッキングリストに記載されている商品をピッキングし忘れてしまうケースも考えられます。
ダブルチェックの重要性も無視できません。
ダブルチェックが適切に行われていない場合、ミスを発見することができず、そのまま出荷されてしまう可能性があります。
特に、目視によるダブルチェックは、作業者の集中力や注意力に依存するため、どうしてもミスを見逃してしまうリスクがあります。
これらの問題を解決するためには、情報共有の徹底とダブルチェックの制度化が不可欠です。
作業者間で正確な情報を共有するための仕組みを構築し、ピッキングリストの情報を常に最新の状態に保つことが重要です。また、ダブルチェックの方法を明確化し、ダブルチェックを行う担当者を定めることも必要です。
さらに、ダブルチェックの結果を記録することで、ミスが発生した原因を分析し、再発防止に役立てることができます。
ピッキングミスによる悪影響
顧客からの信用低下
ピッキングミスが繰り返されると、顧客からの信用を失い、取引停止につながる可能性があります。
特に、誤出荷は企業の評判を大きく損なう可能性があります。
顧客は、正確で迅速な商品の納品を期待しています。
もし、ピッキングミスによって誤った商品が届けられたり、注文した商品が不足していたりすると、顧客は企業に対する不信感を抱くでしょう。そのような状況が繰り返されると、顧客は他の企業に乗り換えてしまう可能性が高まります。
特に、ECサイトなどで商品を購入する顧客は、オンラインでの取引に慣れており、商品の正確性や迅速な配送を求めている傾向があります。
したがって、ピッキングミスは、顧客満足度を低下させるだけでなく、企業の売上にも大きな影響を与える可能性があります。
企業の評判が一度損なわれてしまうと、その信頼を回復するには多大な時間と労力がかかります。
顧客の信頼を維持するためには、ピッキングミスを減らすための対策を講じることが非常に重要です。
具体的な対策としては、作業ルールの徹底、作業環境の最適化、そしてデジタルピッキングシステムの導入などが挙げられます。
これらの対策を組み合わせることで、ピッキングミスを大幅に減らすことができ、顧客からの信頼を維持することができます。
作業負担の増加とコスト増大
ピッキングミスが発生すると、修正作業や再出荷の手間が増え、作業負担が増大します。
また、誤出荷による返品や再梱包などのコストも発生します。
ピッキングミスが発生すると、まず、その原因を特定し、誤って出荷された商品を回収する必要があります。その後、正しい商品を再度ピッキングし、出荷し直さなければなりません。
これらの作業は、通常のピッキング作業に加えて行う必要があり、作業者の負担を大幅に増加させます。特に、ピッキングミスが多発している場合、作業者は常に修正作業に追われ、本来の業務に集中することができなくなります。
また、誤出荷による返品や再梱包も、企業にとって大きなコストとなります。
返品された商品は、再度検品し、保管する必要があります。また、再梱包には、梱包材や人件費などのコストがかかります。さらに、誤出荷によって、顧客から返品された商品の価値が下がってしまう可能性もあります。
これらのコストを合計すると、ピッキングミスによる損失は非常に大きくなります。
したがって、ピッキングミスを減らすことは、作業者の負担を軽減するだけでなく、企業のコスト削減にもつながります。
そのためには、ピッキングミスの原因を分析し、具体的な改善策を講じる必要があります。
例えば、作業ルールの徹底や、作業環境の改善、そしてデジタルピッキングシステムの導入などが有効です。
これらの対策を組み合わせることで、ピッキングミスを減らし、作業負担とコストを削減することができます。
生産効率の低下
ピッキングミスにより、生産ラインが停止したり、遅延が発生したりすると、全体的な生産効率が低下します。
また、ミスを修正するための時間も、生産時間を圧迫します。
例えば、生産ラインで必要な部品がピッキングミスによって不足している場合、生産ラインは停止せざるを得ません。
生産ラインが停止すると、その間、製品の生産ができなくなり、納期遅延につながります。また、生産ラインの停止によって、他の作業工程にも影響が及び、生産全体の効率が低下する可能性があります。
さらに、ピッキングミスを修正するための時間も、生産時間を圧迫します。
ミスを発見した後、正しい部品を再度ピッキングし、生産ラインに供給する必要があるため、その間に生産活動は中断されます。
この中断時間が増えるほど、生産効率は低下します。
ピッキングミスは、生産効率を低下させるだけでなく、生産コストの増加にもつながります。
生産ラインが停止したり、遅延したりすると、人件費や設備費などの固定費が無駄になってしまいます。また、納期遅延によって、顧客からの信頼を失ってしまう可能性もあります。
これらの問題を解決するためには、ピッキングミスを減らすための対策を講じることが重要です。
例えば、作業ルールの徹底、作業環境の最適化、そしてデジタルピッキングシステムの導入などが有効です。
これらの対策を組み合わせることで、ピッキングミスを減らし、生産効率を向上させることができます。
さらに、ピッキングミスが発生した場合に、迅速に修正するための仕組みを整備することも重要です。
ピッキングミスを減らすための具体的な改善策
デジタルピッキングシステムの導入
タカハタ電子のデジタルピッキングシステムのような、ミスを減らすためのテクノロジーを導入すると、作業者の負担を軽減し、ピッキング精度を向上させることができます。
デジタルピッキングシステムは、ピッキング作業をデジタル化し、作業者が行うべき作業を正確に指示するシステムです。
例えば、ピッキングする商品の棚に設置されたランプが点灯し、作業者はそのランプに従って商品を取り出すことで、ピッキングミスを減らすことができます。
また、デジタルピッキングシステムは、ピッキングした商品の個数を自動でカウントしたり、ピッキング作業の進捗状況をリアルタイムで確認したりすることも可能です。
これらの機能によって、作業者はより効率的にピッキング作業を行うことができます。
デジタルピッキングシステムの導入は、ピッキング作業の効率化だけでなく、作業者の負担軽減にもつながります。
従来のピッキング作業では、作業者はピッキングリストを見ながら、棚から商品を探し出す必要がありました。しかし、デジタルピッキングシステムでは、ランプが点灯した棚から商品を取り出すだけでよいため、作業者の負担を大幅に軽減することができます。
さらに、デジタルピッキングシステムは、ピッキングミスの原因を分析する機能も備えています。
例えば、どの棚でピッキングミスが多いのか、どの時間帯にピッキングミスが多いのかなどを分析することで、ピッキングミスの原因を特定し、再発防止策を講じることができます。
これらの利点から、デジタルピッキングシステムは、ピッキングミスを減らすための非常に有効な手段です。
ただし、導入には初期費用がかかるため、費用対効果を十分に検討する必要があります。
作業環境の最適化
棚や商品の配置を見直し、類似品を離して配置することで、ピッキングミスを減らすことができます。
また、作業スペースを整理整頓し、作業者が動きやすい環境を整えることも重要です。
棚や商品の配置は、ピッキング作業の効率に大きく影響します。
例えば、よくピッキングされる商品を、作業者が手の届きやすい場所に配置したり、類似品を離して配置したりすることで、ピッキングミスを減らすことができます。また、棚の高さを調整することで、作業者が無理な姿勢でピッキング作業を行う必要がなくなり、疲労を軽減することができます。
作業スペースの整理整頓も非常に重要です。
作業スペースが散らかっていると、作業者はスムーズに移動することができず、ピッキング作業の効率が低下します。また、床に物が散乱していると、作業者がつまずいて怪我をするリスクもあります。
作業スペースを整理整頓し、作業者が動きやすい環境を整えることで、ピッキング作業の効率を向上させ、ミスを減らすことができます。
具体的には、不要なものを処分したり、棚や収納ボックスを活用したりすることで、作業スペースを広く確保することができます。
さらに、作業者が使用する道具や機器を整理整頓することで、作業効率を向上させることができます。
また、作業スペースの照明を明るくすることも重要です。
照明が暗いと、作業者は商品を正確に識別することが難しくなり、ピッキングミスが発生しやすくなります。
これらの対策を講じることで、作業環境を最適化し、ピッキングミスを減らすことができます。
作業マニュアルの作成と徹底
作業マニュアルを作成し、作業者に徹底することで、ピッキング方法のばらつきをなくし、ミスを減らすことができます。
また、定期的な見直しと改善も必要です。
作業マニュアルは、ピッキング作業の手順や注意点などを明確に記載したものです。
作業マニュアルを作成することで、作業者は誰でも同じ方法でピッキング作業を行うことができるようになり、ピッキング方法のばらつきをなくすことができます。
また、作業マニュアルには、ピッキングミスが発生しやすい箇所や、注意すべき点なども記載することで、ピッキングミスを減らすことができます。
作業マニュアルを作成する際には、作業者からの意見を取り入れ、現場の実態に即した内容にすることが重要です。
作業マニュアルは、作成したら終わりではなく、定期的に見直しと改善を行う必要があります。
ピッキング作業の効率を向上させるためには、作業者の意見を参考に、常に改善を繰り返す必要があります。
例えば、新しい商品が入荷した場合や、ピッキング方法が変更になった場合には、作業マニュアルを更新する必要があります。
また、作業マニュアルの内容を定期的に見直し、作業者が理解しやすい内容になっているかを確認する必要があります。
作業マニュアルを徹底するためには、作業者への教育と訓練が不可欠です。
作業者に対して、作業マニュアルの内容を十分に説明し、実際に作業を行わせることで、作業マニュアルの理解度を高めることができます。
また、定期的に作業マニュアルの確認テストを実施することで、作業者が作業マニュアルの内容をしっかりと理解しているかを確認することができます。
これらの対策を講じることで、作業マニュアルを徹底し、ピッキングミスを減らすことができます。
倉庫管理システム(WMS)の活用
倉庫管理システム(WMS)を導入することで、ロケーション管理の精度を高め、ピッキング作業の効率を向上させることができます。
WMSは、商品の入出庫、在庫管理、ロケーション管理など、倉庫内の業務を効率化するためのシステムです。
WMSを導入することで、商品の保管場所や在庫状況をリアルタイムで把握することができ、ピッキング作業を効率化することができます。
例えば、WMSは、ピッキングリストを自動で生成したり、ピッキング作業の進捗状況をリアルタイムで確認したりする機能があります。
これらの機能によって、作業者はより効率的にピッキング作業を行うことができます。
また、WMSは、ロケーション管理の精度を高めることができます。
WMSによって、商品の保管場所を正確に管理することで、ピッキング作業時に商品を探す手間を減らし、ピッキングミスを減らすことができます。
さらに、WMSは、在庫管理の精度を高めることもできます。
WMSによって、在庫数を正確に把握することで、欠品や過剰在庫を防ぎ、無駄なコストを削減することができます。
WMSを導入する際には、自社の倉庫の規模や業務内容に合わせて、適切なシステムを選ぶ必要があります。
また、WMSの導入には、初期費用がかかるため、費用対効果を十分に検討する必要があります。
ただし、WMSを導入することで、ピッキング作業の効率化やロケーション管理の精度向上など、多くのメリットを得ることができます。
これらの利点から、WMSは、ピッキングミスを減らすための非常に有効な手段と言えるでしょう。
導入後も、システムの運用状況を定期的に見直し、改善を繰り返すことが重要です。
関連情報の共有とダブルチェックの徹底
ピッキングリストを見やすく改善したり、同梱物をバーコードで管理したりすることで、ミスを減らすことができます。
また、ダブルチェックを徹底することで、ヒューマンエラーを防止することができます。
ピッキングリストは、作業者がピッキングを行うための指示書です。
ピッキングリストが見にくいと、作業者はピッキングミスを起こしやすくなります。
例えば、文字が小さかったり、情報が整理されていなかったりすると、作業者は誤った商品をピッキングしてしまう可能性があります。
ピッキングリストを改善することで、ピッキングミスを減らすことができます。
具体的には、文字を大きくしたり、情報を整理したり、色分けしたりすることで、ピッキングリストを見やすくすることができます。
同梱物の管理も、ピッキングミスを減らす上で重要です。
同梱物をバーコードで管理することで、ピッキング作業時に同梱物を確認する手間を省くことができ、ピッキングミスを減らすことができます。
また、バーコードで管理することで、どの同梱物をどの商品に同梱すればよいのかを正確に把握することができます。
ダブルチェックも、ピッキングミスを減らす上で不可欠な手段です。
ダブルチェックを徹底することで、作業者が誤った商品をピッキングした場合でも、出荷前にミスを発見することができます。
ダブルチェックの方法は、作業者によって異なることがないように、明確に定める必要があります。
また、ダブルチェックを行う担当者を定めることも重要です。
これらの対策を講じることで、ピッキングミスを減らし、出荷品質を向上させることができます。
まとめ:ピッキングミス削減は継続的な改善が必要
ピッキングミスの削減には、原因の分析、具体的な改善策の実行、そして継続的な見直しが不可欠です。
デジタルピッキングシステムやWMSなどのテクノロジーを導入し、作業環境とルールを最適化することで、ピッキングミスを大幅に減らし、生産効率を向上させることができます。実績班長のようなツールも有効です。
ピッキングミスは、顧客からの信用低下、作業負担の増加、コスト増大、生産効率の低下など、企業にとって様々な悪影響をもたらします。
これらの悪影響を最小限に抑えるためには、ピッキングミスを減らすための対策を講じることが不可欠です。
ピッキングミスの原因は、作業ルール不徹底、人為的ミス、不適切なロケーション、作業環境、情報共有の不足など、多岐にわたります。
これらの原因を特定し、それぞれに適した対策を講じる必要があります。
例えば、作業ルールの徹底、作業環境の最適化、デジタルピッキングシステムの導入、WMSの活用、ダブルチェックの徹底などが挙げられます。
これらの対策を組み合わせることで、ピッキングミスを大幅に減らすことができます。
ただし、これらの対策は一度実行すれば終わりではありません。
ピッキングミスを減らすためには、継続的な改善が必要です。
例えば、定期的にピッキングミスの原因を分析し、改善策を見直したり、新しい技術を導入したりする必要があります。
また、作業者からのフィードバックを積極的に収集し、改善策に反映させることも重要です。
ピッキングミスを減らすための努力は、企業の成長と発展に不可欠なものです。
これらの対策を講じることで、ピッキングミスを減らし、顧客満足度の向上、コスト削減、生産効率の向上など、多くのメリットを得ることができます。
さらに、従業員の満足度向上にもつながるでしょう。実績班長のようなツールを活用すると、これらの活動が円滑に進むでしょう。
常に改善を意識し、より良いピッキング作業を目指しましょう。