棚卸しでの在庫トラブルを解消!主な原因7選とWMS導入による解決策
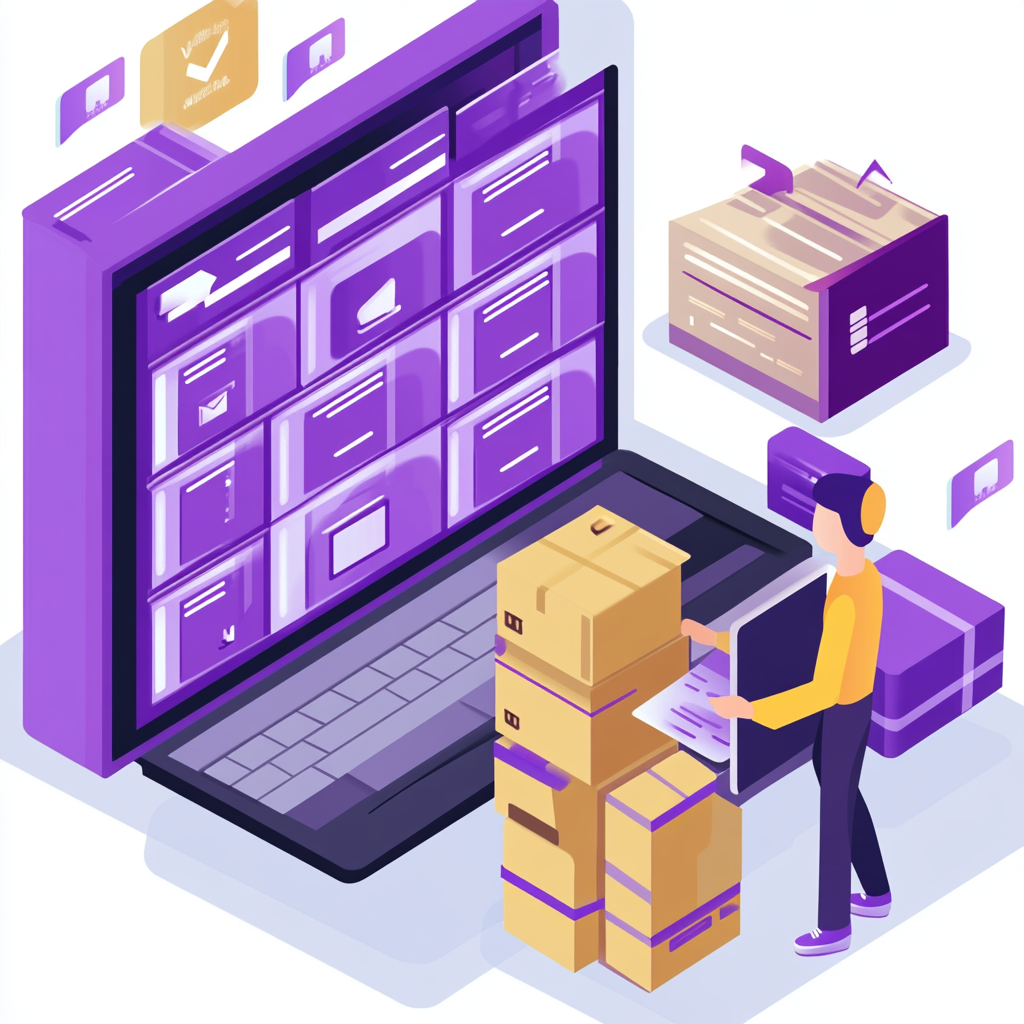
棚卸しは在庫管理の重要なプロセスですが、様々なトラブルが発生しやすいのも事実です。
この記事では、棚卸しでよくある在庫トラブルの主な原因7つを解説し、WMS(倉庫管理システム)導入による解決策と物流改善のヒントをご紹介します。
この記事では、棚卸し作業で発生する在庫トラブルの主な原因を7つに絞り、それぞれの問題点と具体的な事例を詳しく解説します。
さらに、これらの問題を解決するための有効な手段として、WMS(倉庫管理システム)の導入がどのように役立つのか、その具体的な機能やメリットを掘り下げてご紹介します。
また、WMS導入だけでなく、物流改善やテクノロジーの活用がいかに棚卸しの精度向上に貢献するのかについても詳しく説明し、読者の皆様がより正確で効率的な在庫管理を実現するための実践的な知識を提供します。
棚卸しでよくある在庫トラブル7つの原因
棚卸しは、企業の在庫管理において非常に重要なプロセスであり、定期的に実施することで、帳簿上の在庫数と実際の在庫数を照合し、差異を発見・修正する目的があります。
しかし、この作業は人手で行われることが多く、様々な要因で在庫数に誤差が生じやすいのが現状です。在庫数のずれは、企業の経営に悪影響を及ぼすだけでなく、顧客満足度の低下にも繋がる可能性があります。
棚卸しにおける在庫トラブルの原因を理解し、適切な対策を講じることが、効率的な在庫管理と企業全体の成長にとって不可欠です。
数え間違いや記録ミス
棚卸し作業における人為的なミスは、在庫数の誤差を生む大きな要因です。
特に手作業での棚卸しは、数え間違いや記録ミスが起こりやすく、正確な在庫把握を妨げます。
例えば、棚卸し時に複数の商品をまとめて数えてしまい、正確な数を把握できなくなるケースや、記録時に数字を誤って転記してしまうケースなどが挙げられます。
このような人為的なミスは、棚卸し結果の信頼性を大きく損なう原因となります。
具体的な例として、過去には、棚卸し作業員が商品の種類を誤認し、別の商品の数を誤ってカウントしてしまう事例がありました。また、棚卸し結果を記録する際に、数字の桁を間違えて記入してしまい、実際の在庫数と大きな差異が生じたというケースも報告されています。これらのミスは、特に繁忙期や人員不足の際に発生しやすく、企業にとっては大きな課題となります。
人為的なミスは、棚卸しの歴史において常に課題でした。初期の在庫管理は、すべて手作業で行われていたため、ミスを完全に防ぐことは不可能に近かったです。
記録媒体も紙ベースが中心であったため、情報の整理や転記の過程で多くのミスが発生しました。
その後、コンピューターの導入によってデジタル化が進みましたが、それでも入力ミスや操作ミスなどの人為的な要因による誤差は依然として存在し続けています。
現代においても、棚卸し作業における人為的ミスの防止は、在庫管理の重要なテーマの一つであり、多くの企業がその対策に力を入れています。
商品の破損や紛失
保管場所の不備や、作業中の不注意によって、商品が破損したり、紛失したりすることがあります。
このような物理的な問題も棚卸し時の誤差に繋がります。
例えば、保管中に商品が落下して破損したり、棚卸し作業中に商品が紛失したりするケースがあります。
また、破損した商品を適切に処理せずにそのまま放置してしまうと、棚卸し時に在庫数と実数が合わなくなる原因となります。
具体例として、倉庫内でフォークリフトが誤って商品を破損させてしまったり、棚卸し作業中に商品が棚から落下し破損、その後、破損した商品が適切に処分されずに在庫数から差し引かれず、棚卸し時に差異が発生するという事例が挙げられます。また、一部の商品が保管場所から移動された後、元の場所に戻されず、結果として紛失扱いになってしまうケースも少なくありません。
このような物理的な損傷や紛失は、在庫管理の正確性を大きく損なうだけでなく、企業の損失にも繋がります。
商品の破損や紛失は、物流の歴史の中で常に存在した問題です。初期の輸送手段が未発達だった時代には、商品の破損や紛失が頻繁に発生しており、物流コストを押し上げる要因となっていました。
また、保管技術が未熟だった時代には、湿気や害虫などによる商品の劣化や破損も多く見られました。近代に入り、物流技術や保管技術が向上したものの、完全に破損や紛失を防ぐことは難しく、常に改善を求めるべき課題として存在しています。
これらの問題を解決するため、梱包方法の見直しや、倉庫内の環境整備など、様々な対策が講じられてきました。
ロケーション管理の不徹底
商品の保管場所が適切に管理されていない場合、棚卸し作業時に商品を見つけることが困難になり、棚卸し漏れや二重カウントが発生する原因となります。
例えば、商品が整理されずに乱雑に置かれている場合、棚卸し作業時にどこに何があるのか把握するのが難しく、商品の数え漏れや二重カウントが発生しやすくなります。
また、ロケーションが明確でないと、棚卸し担当者が商品を特定するのに時間がかかり、作業効率が低下する要因にもなります。
例えば、倉庫内のロケーションが曖昧なまま商品を保管すると、棚卸し時に商品を探し出すのに時間がかかったり、同じ商品を重複して数えてしまったりするケースがあります。過去には、商品が保管場所から移動されたにも関わらず、記録が更新されず、棚卸し時に大きな差異が生じたという事例も報告されています。このようなロケーション管理の不徹底は、棚卸し作業の効率を著しく低下させるだけでなく、在庫の正確性にも大きな影響を与えます。
ロケーション管理の不徹底は、在庫管理の初期段階から存在する問題でした。手作業で在庫管理を行っていた時代には、商品がどこに保管されているかを把握することが難しく、棚卸し作業が非常に煩雑でした。その後、棚札やロケーション表示板などが導入されましたが、それだけでは不十分であり、人的ミスによるロケーション管理の不徹底は依然として大きな課題でした。
現代においては、バーコードやRFIDなどの技術を活用したロケーション管理システムが普及し、効率的な在庫管理を支援していますが、これらの技術を適切に運用しなければ、ロケーション管理の不徹底という課題を完全に克服することは難しいのが現状です。
上記以外にも、棚卸し時に発生する在庫トラブルの原因は多岐にわたります。
例えば、出荷待ちの商品が誤って棚卸しの対象に含まれてしまったり、返品された商品が適切な場所に保管されずに紛れてしまったりするケースも考えられます。また、季節変動や需要予測の誤りによる過剰在庫や欠品も、棚卸し時の誤差を引き起こす原因となり得ます。さらに、担当者の経験不足や教育不足も、棚卸しの精度に影響を与える要因となります。
これらの問題を総合的に捉え、対策を講じることが、より正確な在庫管理を実現するために重要です。
WMS導入で在庫トラブルを解決
WMS(Warehouse ManagementSystem)は、倉庫内の在庫管理を効率化し、正確性を高めるためのシステムです。WMSを導入することで、棚卸し作業における多くの課題を解決し、在庫トラブルの発生を大幅に抑制することが可能になります。
WMSは、入庫、出庫、棚卸し、ロケーション管理など、倉庫業務全般をデジタル化し、リアルタイムで在庫情報を把握することを可能にします。その結果、人為的なミスを減らし、作業効率を向上させ、在庫の可視化を実現します。以下に、WMS導入によってどのように在庫トラブルが解決されるのか、具体的な機能とその効果について詳しく説明していきます。
リアルタイムな在庫情報把握
WMSを導入することで、入庫・出庫データがリアルタイムで反映され、正確な在庫情報を常に把握できます。
これにより、棚卸し時の誤差を大幅に減らすことが可能です。
WMSでは、商品の入庫や出庫の際に、データをシステムに登録することで、常に最新の在庫数が把握できます。
これにより、棚卸し作業時に、実際の在庫数とシステム上の在庫数のずれを最小限に抑えることができ、正確な在庫管理が可能になります。
具体的には、WMSは、商品の入庫時にバーコードやRFIDなどの自動認識技術を利用してデータを記録し、その情報を瞬時にシステムに反映させます。同様に出庫時にも、商品をスキャンすることで、在庫数が自動的に減算されます。これにより、手作業による入力ミスや転記ミスを排除し、常に最新の在庫情報をシステム上で確認することができます。また、リアルタイムで在庫情報を把握できるため、棚卸しの頻度を減らすことができ、業務効率の向上にもつながります。
WMSの歴史は、コンピューター技術の発展とともに進化してきました。初期のWMSは、主に大型の倉庫や物流センターで使用され、メインフレームコンピューターで動作していました。
これらのシステムは、データ入力や処理に時間がかかり、操作も複雑でした。
しかし、1990年代に入り、パーソナルコンピューターの普及やインターネットの登場によって、WMSはより手軽に利用できるシステムへと変化しました。
クラウド型のWMSが登場したことで、中小企業でもWMSを導入しやすくなり、在庫管理の効率化に大きく貢献しています。現在では、AIや機械学習などの最新技術を取り入れたWMSも開発され、より高度な在庫管理が可能になっています。
ハンディターミナルによる作業効率化
ハンディターミナルとWMSを連携させることで、バーコードスキャンによる棚卸しが可能になり、入力ミスや作業時間を大幅に削減できます。
インターストックのようなWMSでは、この機能が充実しています。
ハンディターミナルを使用することで、商品のバーコードをスキャンするだけで、自動的に在庫数がカウントされ、システムに記録されます。
これにより、手入力によるミスをなくし、作業時間も大幅に短縮することができます。また、インターストックのようにWMSと連携することで、より効率的な棚卸し作業が可能となります。
ハンディターミナルは、バーコードやQRコードを読み取ることで、商品の情報を瞬時にシステムに送信する機能を持っています。この機能を利用することで、棚卸し作業員は、商品のバーコードをスキャンするだけで、在庫数を自動的にシステムに登録することができます。
これにより、手作業によるカウントミスや記録ミスを防ぎ、正確な在庫管理を実現することができます。また、ハンディターミナルの活用は、棚卸し作業時間を大幅に短縮し、人員コストの削減にも貢献します。
インターストックのようなWMSでは、ハンディターミナルとの連携機能が強化されており、より効率的な棚卸し作業をサポートします。
ハンディターミナルは、1970年代に登場し、当初は主にPOSシステムで使用されていました。
その後、バーコード技術の普及とともに、物流業界でも活用されるようになりました。初期のハンディターミナルは、サイズが大きく、操作も複雑でしたが、技術の進歩とともに、小型化・軽量化が進み、使いやすくなりました。
現在では、無線LANやBluetoothなどの通信機能を搭載したモデルも登場し、WMSとの連携がよりスムーズになっています。ハンディターミナルの進化は、棚卸し作業の効率化に大きく貢献し、現代の物流現場では欠かせないツールとなっています。
在庫分析機能の活用
WMSの在庫分析機能を活用することで、滞留在庫や過剰在庫を可視化し、棚卸し時の確認ポイントを絞り込むことができます。
これにより、棚卸し作業を効率化し、誤差を減らすことができます。
在庫分析機能により、売れ残っている商品や、過剰に在庫を抱えている商品を特定できます。
これらの商品に焦点を当てて棚卸しを行うことで、作業時間を短縮し、より効率的な棚卸しを実現できます。
また、過剰在庫を把握することで、発注量の見直しや在庫処分などの対策を講じることも可能です。
WMSの在庫分析機能は、過去の販売データや入出庫データに基づいて、在庫の動きを詳細に分析します。これにより、売れ筋商品、滞留商品、過剰在庫などを特定し、グラフや表で可視化することができます。この情報をもとに、棚卸し作業の優先順位を決定したり、特定の商品に焦点を当てて確認作業を行ったりすることが可能です。
また、在庫分析の結果は、発注量の調整や在庫処分の判断にも役立ち、在庫の最適化に貢献します。
WMSの在庫分析機能は、棚卸し作業の効率化だけでなく、在庫管理全体の精度を高める上で重要な役割を果たします。
在庫分析の歴史は、統計学やデータ分析技術の発展とともに進化してきました。
初期の在庫分析は、手作業でデータを集計し、簡単なグラフを作成するといったものでした。
その後、コンピューターの普及により、より複雑な分析が可能になり、Excelなどの表計算ソフトが活用されるようになりました。近年では、AIや機械学習などの最新技術を用いた高度な在庫分析が実現され、需要予測や在庫最適化に役立てられています。WMSに搭載された在庫分析機能は、これらの技術を活用し、より効率的で正確な在庫管理を支援します。
WMS導入は、単に棚卸し作業を効率化するだけでなく、在庫管理全体の精度を向上させるための重要なステップです。
リアルタイムでの在庫情報把握、ハンディターミナルによる作業効率化、在庫分析機能の活用を通じて、在庫トラブルの発生を大幅に抑制し、企業の損失を減らすことができます。また、WMSの導入は、より戦略的な在庫管理を可能にし、企業の競争力強化にも繋がります。
WMSを導入することで、企業の物流コスト削減と利益拡大の両立を実現することができるでしょう。
物流改善で棚卸し精度を向上
WMSの導入と並行して、物流現場における改善活動も、棚卸しの精度向上に不可欠です。単にシステムを導入するだけでなく、現場の作業プロセスを見直し、最適化することで、より効果的な在庫管理を実現することができます。
物流改善は、棚卸し作業だけでなく、入庫、出庫、保管など、倉庫業務全般の効率化に貢献します。以下に、棚卸し精度を向上させるための具体的な物流改善策について説明していきます。
ロケーション管理の徹底
棚卸しの精度を向上させるには、ロケーション管理の徹底が不可欠です。
商品の保管場所を明確にし、定期的な見直しを行うことで、棚卸し作業をスムーズに進めることができます。
ロケーション管理を徹底することで、どの商品がどこにあるのかが一目でわかり、棚卸し時に商品を探す手間を省けます。
また、定期的にロケーションを見直すことで、保管場所が最適化され、商品の出し入れがスムーズになり、紛失のリスクを減らすことも可能です。
これにより、棚卸し作業時間の短縮と、精度の向上が期待できます。
ロケーション管理を徹底するためには、まず、倉庫内の各場所に明確な住所を割り当てる必要があります。そして、商品の入庫時に、どの商品をどこに保管したのかをシステムに記録し、保管場所を明確に表示します。
また、定期的にロケーションを見直し、商品の保管状況に合わせて最適な場所に配置します。さらに、ロケーションの変更があった場合には、必ずシステムを更新し、最新の情報が反映されるようにします。
これにより、棚卸し時に商品を探す時間を大幅に短縮し、作業効率を向上させることができます。また、ロケーション管理の徹底は、商品の紛失や破損リスクを減らす効果も期待できます。
ロケーション管理を徹底するためには、5S(整理、整頓、清掃、清潔、躾)の徹底や、ABC分析による商品の配置最適化なども有効です。また、ロケーション管理のルールを明確にし、従業員への教育を徹底することも重要です。
ロケーション管理の徹底は、棚卸し作業だけでなく、ピッキング作業の効率化にも繋がります。これにより、倉庫業務全体の効率性が向上し、より正確な在庫管理が可能になります。
棚卸し作業手順の見直し
棚卸し作業手順を見直し、作業マニュアルを作成することで、作業員の経験やスキルに関わらず、一定の品質で棚卸し作業を行うことができます。
作業マニュアルを作成することで、棚卸し作業の標準化が可能になります。
これにより、作業員の経験やスキルに関わらず、誰でも同じ品質で棚卸し作業を行うことができるようになり、結果として、棚卸し時の誤差を減らすことができます。また、作業手順が明確になることで、作業時間も短縮できる可能性があります。
棚卸し作業手順を見直す際には、まず現状の作業フローを詳細に分析し、課題点を洗い出す必要があります。そして、課題点を解決するための最適な作業手順を設計し、マニュアルを作成します。マニュアルには、棚卸し作業の目的、手順、注意事項などを具体的に記述し、誰でも理解できるようにする必要があります。
また、マニュアルは定期的に見直し、改善を行うことが重要です。作業マニュアルを作成し、従業員への教育を徹底することで、棚卸し作業の精度が向上し、作業時間の短縮にもつながります。棚卸し作業の標準化は、ヒューマンエラーを減らし、より正確な在庫管理を実現するために非常に重要です。
棚卸し作業手順の見直しは、単に効率化のためだけでなく、作業員の負担を減らすことにも繋がります。明確な作業手順を示すことで、作業員の迷いや不安を解消し、よりスムーズな作業を可能にします。また、作業手順を標準化することで、新人教育のコストを削減し、チーム全体の生産性を高める効果も期待できます。定期的な作業手順の見直しと改善は、より質の高い棚卸し作業を実現し、企業の競争力強化に貢献します。
物流改善は、棚卸し作業の精度向上だけでなく、倉庫業務全体の効率化に貢献する重要な取り組みです。ロケーション管理の徹底、棚卸し作業手順の見直し、従業員の教育などを通じて、より正確で効率的な在庫管理を実現することができます。
物流改善は、単にコスト削減だけでなく、顧客満足度の向上にも繋がり、企業の競争力強化にも貢献します。継続的な改善活動を通じて、より質の高い物流体制を構築することが、企業の成長に不可欠であると言えるでしょう。
テクノロジーを活用した棚卸しの効率化
WMSの導入や物流改善に加えて、最新のテクノロジーを活用することで、棚卸し作業をさらに効率化し、精度を高めることが可能です。IoTデバイスやAI技術などの進歩は、在庫管理に新たな可能性をもたらしています。これらのテクノロジーを積極的に導入することで、人手による作業を大幅に減らし、リアルタイムでの在庫把握を可能にします。
以下に、テクノロジーを活用した棚卸しの効率化について、具体的な事例を交えて説明していきます。
スマートマットクラウドによる在庫管理
スマートマットクラウドのようなIoT機器を導入することで、リアルタイムでの在庫量把握が可能になり、棚卸し作業を自動化できます。
これにより、作業時間や人件費を削減し、より正確な在庫管理が実現します。
スマートマットクラウドは、商品の下に設置するだけで、リアルタイムで在庫量を計測できるIoT機器です。
これにより、棚卸し作業を自動化でき、作業員が棚卸しのために倉庫内を歩き回る必要がなくなり、大幅な時間短縮と人件費削減につながります。
また、リアルタイムで在庫量が把握できるため、欠品や過剰在庫のリスクを減らし、より正確な在庫管理を実現できます。
スマートマットクラウドは、マット型のセンサーを商品の下に設置するだけで、重量を計測し、そのデータをクラウドに送信します。これにより、リアルタイムで在庫量を把握し、自動的に棚卸しを行うことができます。
従来の棚卸し作業では、作業員が倉庫内を歩き回り、商品の数を数える必要がありましたが、スマートマットクラウドを導入することで、その手間を大幅に削減できます。また、リアルタイムで在庫量が把握できるため、欠品や過剰在庫の早期発見が可能になり、迅速な対応を取ることができます。スマートマットクラウドは、人件費の削減、作業時間の短縮、在庫管理の精度向上に大きく貢献します。
IoT(Internet ofThings)技術の歴史は、センサー技術や通信技術の進歩とともに発展してきました。初期のIoTデバイスは、主に産業用途で使用されていましたが、近年では一般家庭でも広く利用されるようになりました。物流業界では、スマートマットクラウドのようなIoTデバイスを活用することで、リアルタイムでの在庫管理が可能になり、より効率的な物流オペレーションを実現しています。今後もIoT技術はさらに発展し、在庫管理の分野においても新たな可能性を切り開いていくでしょう。
スマートマットクラウド以外にも、RFID(無線周波数識別)タグやドローンを活用した在庫管理など、様々なテクノロジーが棚卸し作業の効率化に貢献しています。RFIDタグは、商品に貼り付けることで、離れた場所からでも商品の情報を読み取ることができ、棚卸し作業の大幅な時間短縮に繋がります。
また、ドローンを活用することで、高所にある商品や、広大な倉庫内の在庫を効率的に把握することが可能です。これらのテクノロジーを組み合わせることで、より高度な在庫管理システムを構築することができます。また、AIや機械学習を活用した需要予測や在庫最適化なども進んでおり、在庫管理の未来はさらに進化していくと考えられます。
テクノロジーの活用は、棚卸し作業の効率化だけでなく、在庫管理全体の精度を向上させる上で非常に重要な要素です。スマートマットクラウドのようなIoT機器、RFIDタグ、ドローンなどのテクノロジーを導入することで、人手による作業を減らし、リアルタイムでの在庫把握を可能にします。また、AIや機械学習などの技術を活用することで、より高度な在庫分析や需要予測が可能になり、在庫最適化を実現できます。
これらのテクノロジーを積極的に導入し、常に最新の技術を取り入れていくことが、競争の激しい現代の物流業界において生き残るための鍵となります。
まとめ
棚卸しの在庫トラブルは、WMS導入と物流改善によって大幅に解決可能です。
インターストックやスマートマットクラウドのようなソリューションを活用し、より正確で効率的な在庫管理を目指しましょう。
WMSの導入により、リアルタイムでの在庫把握や作業効率化が可能になり、棚卸し時の誤差を大幅に減らすことができます。また、ロケーション管理の徹底や作業手順の見直しなどの物流改善と組み合わせることで、より効果的な棚卸しが可能になります。
スマートマットクラウドのようなIoT機器の導入も、棚卸し作業の自動化に貢献し、人件費の削減と在庫管理の精度向上に繋がります。
これらのソリューションを活用し、より正確で効率的な在庫管理を目指すことが、今後の物流業界にとって重要な課題となります。
棚卸しにおける在庫トラブルは、人為的なミス、商品の破損や紛失、ロケーション管理の不徹底など、様々な要因によって発生します。これらの問題を解決するためには、WMSの導入、物流改善、テクノロジーの活用を組み合わせた総合的なアプローチが不可欠です。
WMSは、リアルタイムでの在庫情報把握、ハンディターミナルによる作業効率化、在庫分析機能の活用など、在庫管理を効率化するための多くの機能を提供します。
また、ロケーション管理の徹底や作業手順の見直しなどの物流改善は、現場の作業効率を向上させ、ヒューマンエラーを減らす上で重要です。さらに、スマートマットクラウドのようなIoT機器を導入することで、棚卸し作業を自動化し、人件費を削減することができます。
これらの取り組みを継続的に行うことで、より正確で効率的な在庫管理を実現し、企業の競争力強化に繋げることができます。今後は、AIや機械学習などの最新技術を積極的に導入し、在庫管理の高度化をさらに進めていく必要があります。
今後、物流業界においては、サプライチェーン全体の最適化が重要な課題となります。棚卸し作業は、サプライチェーン全体の中で、在庫状況を正確に把握するための重要なプロセスです。
WMS、物流改善、テクノロジーの活用を組み合わせることで、棚卸し作業の精度を向上させ、より効率的なサプライチェーンを構築することが可能になります。
また、環境への配慮や持続可能な物流を実現するための取り組みも重要になります。
今後は、これらの課題を解決するために、より高度な技術やシステムが開発され、導入されていくと考えられます。物流業界の未来は、技術革新と持続可能な社会の実現を両立させることが求められるでしょう。