在庫管理システム(WMS)の役割と選び方を解説
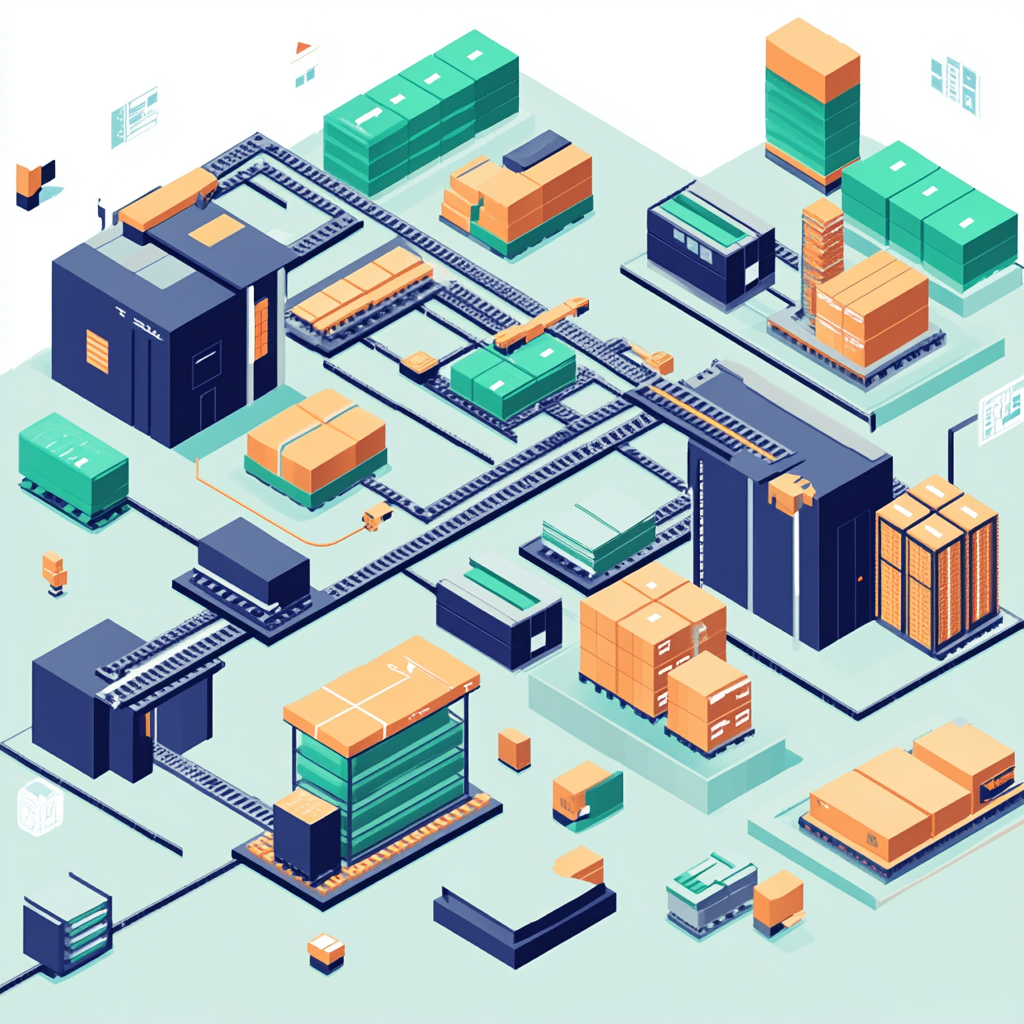
在庫管理システム(WMS)は、効率的な倉庫管理を実現する現代の必須ツールです。本記事では、WMSの基本機能や導入メリット、システム選定のポイントについて詳しく解説します。
在庫管理システム(WMS)とは
WMSの基本機能
在庫管理システム(WMS)は、倉庫や物流センターにおける在庫の管理を効率化するシステムです。倉庫内での商品の入出庫、保管、ピッキング、配送といった一連の業務を統合的に管理し、正確な在庫情報や作業状況をリアルタイムに把握することを可能にします。WMSには、入出庫管理、在庫最適化、リアルタイムの情報可視化、在庫回転率の分析、在庫レベルの管理、在庫の追跡、在庫のロケーション管理、棚卸管理、出荷管理、受注管理、在庫予測、倉庫レイアウトの最適化など、幅広い機能が含まれます。
WMSの進化と影響
従来のWMSは、主に倉庫内での作業効率化を目的としていましたが、近年では、AIやIoT技術の進歩により、より高度な機能が求められるようになっています。最新のWMSは、AIを活用した需要予測や在庫最適化、IoTセンサーによるリアルタイムな在庫状況把握、自動搬送ロボットとの連携、データ分析による在庫管理の改善、音声認識による作業指示など、さらなる効率化と精度向上を実現しています。これらの進化により、企業はより迅速な商品供給、在庫管理コストの削減、顧客満足度の向上、サプライチェーン全体の最適化といった効果を期待できます。
WMSを導入するメリット
作業の効率化とミス削減
WMSは、手作業によるヒューマンエラーを減少させ、業務の標準化を促進します。入出庫作業の自動化、ピッキング作業の効率化、在庫情報の正確な管理などにより、人為的なミスを大幅に削減することができます。また、作業手順の標準化により、作業員のスキル格差によるバラつきを解消し、全体的な作業効率の向上を実現します。WMS導入によって、作業員の負担を軽減し、より快適な作業環境を提供することも可能です。
コストの削減
WMS導入による効率化は、人件費、保管費、輸送費などのコスト削減に貢献します。在庫の過剰な保有や無駄な移動を抑制することで、保管スペースの有効活用や輸送効率の向上を実現できます。また、正確な在庫情報に基づいた発注管理により、過剰な在庫を抱えるリスクを軽減し、在庫管理コストの削減につながります。WMSは、在庫管理の精度を高めることで、在庫の無駄を減らし、コスト削減に貢献します。
リアルタイム情報へのアクセス
WMSでは、在庫状況をリアルタイムで把握できるため、迅速な意思決定が可能です。在庫切れや過剰在庫といった問題を早期に発見し、適切な対応をとることができます。また、リアルタイムな在庫情報に基づいた販売戦略や生産計画の立案が可能となり、ビジネスの迅速化と柔軟性を高めます。WMSは、情報共有を促進し、迅速な意思決定を支援することで、ビジネスの競争力を強化します。
WMS選定のポイント
業界特化型WMSの選択
WMSは、業界や企業規模、業務内容によって最適なものが異なります。例えば、小売業では、販売データとの連携や顧客情報との統合、POSシステムとの連携が重要になります。製造業では、生産計画との連携、部品管理、生産管理システムとの連携が重要になります。物流業では、配送ルートの最適化、配送管理システムとの連携が重要になります。各業界に特化した機能を備えたWMSを選ぶことが、成功につながります。
クラウド型とオンプレミス型の違い
WMSは、導入方法によってクラウド型とオンプレミス型に分けられます。クラウド型は、インターネットを通じてサービスを利用する方式で、初期費用が低く、導入が容易な点が特徴です。また、システムの更新やメンテナンスがベンダーによって行われるため、自社での管理負担が軽減されるというメリットがあります。一方、オンプレミス型は、自社サーバーにシステムを構築する方式で、セキュリティ面で強みがあります。自社でシステムを管理できるため、柔軟なカスタマイズや独自のセキュリティ対策が可能です。企業の規模やセキュリティ要件、システム運用体制、予算などを考慮して、最適な導入方法を選択する必要があります。
WMS導入の成功事例
事例1:小売業での成功事例
ある小売業では、WMS導入により在庫回転率が向上し、売上増加を達成しました。従来は、手作業による在庫管理が中心で、在庫状況の把握に時間がかかっていました。WMS導入により、リアルタイムな在庫情報に基づいた発注管理が可能となり、在庫過剰や在庫不足といった問題を解消しました。その結果、在庫回転率が向上し、売上増加につながりました。さらに、顧客満足度も向上し、リピート率も上昇しました。
事例2:製造業での活用法
製造業においては、WMSのリアルタイム管理機能により、生産計画の柔軟性が向上しています。従来は、生産計画の変更に時間がかかっていましたが、WMS導入により、リアルタイムな在庫情報に基づいた生産計画の変更が可能になりました。その結果、納期遅延や生産停止といった問題を減らし、顧客満足度を高めることに成功しました。また、生産効率も向上し、コスト削減にも貢献しました。
WMS導入の注意点
導入コストの管理
WMS導入には初期費用がかかるため、予算計画が必要です。システムの規模や機能、導入方法によって費用は大きく異なります。導入前に、必要な機能や費用を明確化し、導入後の運用コストも含めた予算計画を立てることが重要です。
導入後のサポート体制
システム導入後のサポート体制を確認することが、運用時のトラブルを防ぎます。システムの運用には、専門的な知識や技術が必要となる場合があり、導入後のサポート体制が充実しているかを確認することが重要です。また、システムのバージョンアップやセキュリティ対策、障害対応など、継続的なサポートが必要となるため、サポート体制がしっかりしているベンダーを選ぶことが重要です。
まとめ:WMSの未来
今後のWMSの展望
AIやIoTとの連携が進む中、次世代のWMSはさらに高機能化が期待されています。AIを活用した需要予測や在庫最適化、IoTセンサーによるリアルタイムな在庫状況把握、自動搬送ロボットとの連携、ドローンによる在庫管理、バーチャルリアリティ技術を用いた倉庫内作業のトレーニングなど、WMSは進化を続け、より高度な機能を提供していくでしょう。これらの進化により、企業はより効率的な在庫管理を実現し、ビジネスの競争力を強化していくことが期待されます。
WMSの歴史
WMSの起源は、1960年代に遡ります。当時、企業は手作業で在庫管理を行っており、在庫の正確な把握や効率的な管理に苦労していました。この問題を解決するために、コンピュータを活用した在庫管理システムが開発されました。初期のWMSは、主に在庫の入出庫管理や在庫状況の把握を目的としていました。 1970年代には、コンピュータの性能向上に伴い、WMSの機能も進化しました。在庫管理に加えて、ピッキングや配送などの作業の効率化を目的とした機能が追加されました。また、バーコードやRFIDなどの技術が導入され、在庫管理の精度が向上しました。 1980年代には、パーソナルコンピュータの普及により、WMSはより身近な存在となりました。中小企業でも導入しやすい価格帯のWMSが登場し、多くの企業がWMSを導入するようになりました。 1990年代には、インターネット技術の発展により、WMSはネットワーク化が進みました。複数の倉庫を連携して管理できるシステムが登場し、より効率的な在庫管理が可能になりました。 2000年代以降は、AIやIoT技術の進歩により、WMSはさらに高度な機能を備えるようになりました。需要予測、在庫最適化、自動搬送ロボットとの連携など、WMSは進化を続け、企業の競争力を強化するための重要なツールとなっています。
WMS導入の成功事例
事例3:EC事業者での成功事例
あるEC事業者では、WMS導入により、受注から出荷までのリードタイムが短縮され、顧客満足度が向上しました。従来は、手作業による受注処理や出荷作業が中心で、処理に時間がかかっていました。WMS導入により、受注処理の自動化、ピッキング作業の効率化、配送ルートの最適化などが実現し、リードタイムが大幅に短縮されました。その結果、顧客満足度が向上し、売上増加にもつながりました。
事例4:物流会社での成功事例
ある物流会社では、WMS導入により、配送効率が向上し、コスト削減を実現しました。従来は、配送ルートの計画や配送状況の管理を手作業で行っていました。WMS導入により、配送ルートの最適化、配送状況のリアルタイム把握、配送員の効率的な配置などが実現し、配送効率が向上しました。その結果、燃料費や人件費などのコスト削減につながりました。
専門家の意見
物流業界の専門家は、「WMSは、企業にとって欠かせないツールになりつつあります。AIやIoT技術の進歩により、WMSはさらに進化し、企業の競争力を強化するための重要な役割を果たすでしょう。」と述べています。 また、ITコンサルタントは、「WMS導入は、企業にとって大きな変革をもたらします。導入前に、自社の業務内容や課題をしっかりと分析し、適切なWMSを選択することが重要です。また、導入後も、継続的な改善や運用体制の構築が不可欠です。」と指摘しています。 WMSは、単なる在庫管理システムではなく、企業のビジネス戦略を支える重要なシステムです。適切なWMSを導入することで、企業は効率的な在庫管理を実現し、ビジネスの競争力を強化することができます。