誤出荷防止の鍵を握る「なぜなぜ分析」とは?効果的な活用法を解説
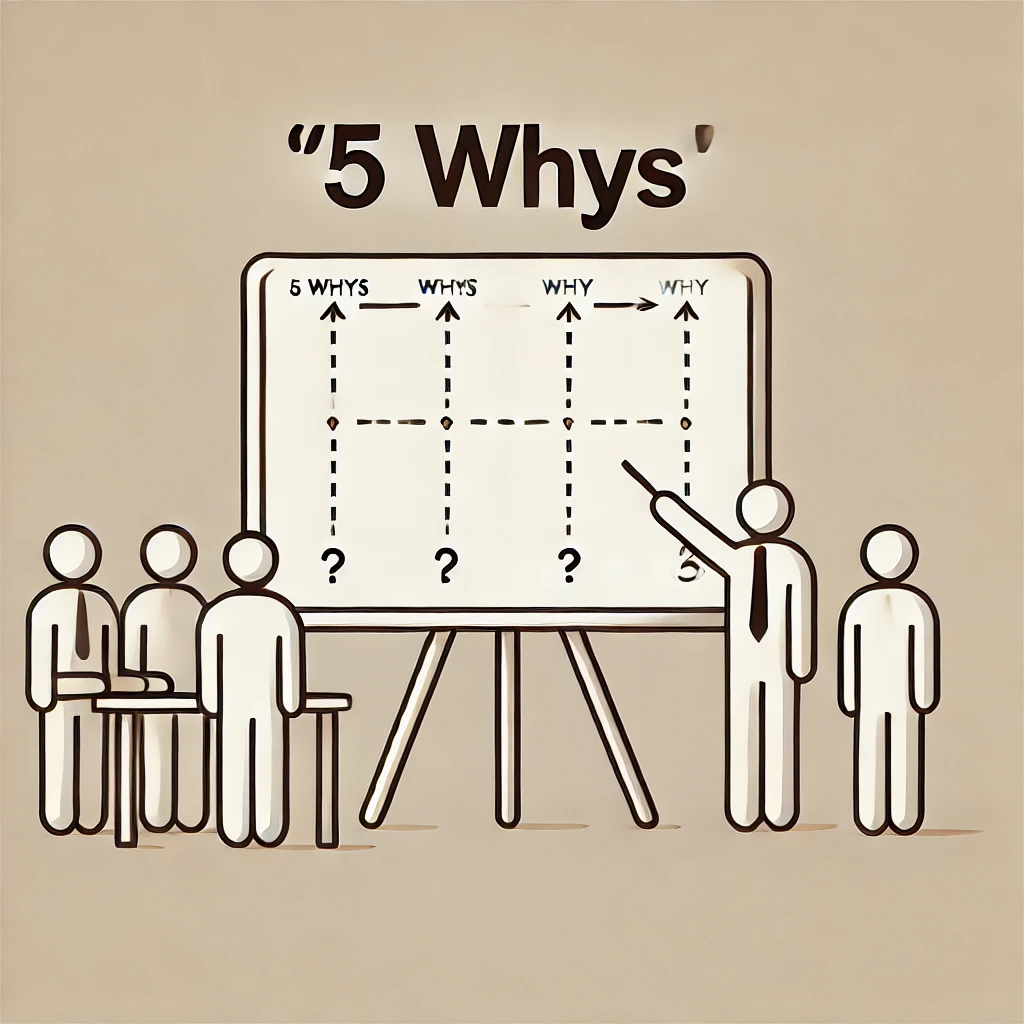
誤出荷が発生すると、企業の信用を失うリスクやコストの増大を引き起こします。そこで役立つのが「なぜなぜ分析」。この記事では、その方法を詳しく解説し、実践的な対策をご紹介します。
誤出荷
商品の誤発送
誤出荷とは、本来届けられるべき商品とは異なる商品が届けられたり、注文した数量と異なる数量の商品が届けられたりするなど、顧客に誤った商品が届いてしまうことを指します。誤出荷は、顧客満足度の低下やブランドイメージの悪化、さらには売上機会の損失など、企業にとって深刻な問題となる可能性があります。
数量ミスが発生
数量ミスは、物流現場におけるピッキング、梱包、発送といった作業で発生するミスの一つで、主に以下のような原因によって引き起こされます。
まず、ピッキングリストの確認不足が挙げられます。ピッキングリストの内容を十分に確認しないまま作業を進めると、誤った商品や数量をピッキングしてしまうリスクが高まります。さらに、作業中の集中力の低下も問題です。同じ作業を長時間続けることで集中力が落ち、注意不足によるミスが増加する可能性があります。
また、作業員のスキル不足も重要な要因です。経験の浅い作業員や適切なトレーニングを受けていない作業員は、数量ミスを犯しやすくなります。一方で、システムエラーも無視できない要素です。在庫管理システムや発注システムに問題が発生すると、正しい数量を反映できず、誤った商品がピッキングされるケースがあります。
作業環境の悪化も数量ミスを引き起こします。例えば、暗い照明や狭い作業スペース、整頓されていない作業エリアでは、作業の正確性が損なわれる可能性があります。
数量ミスを防ぐためには、これらの原因を明確に分析し、適切な対策を講じることが重要です。具体的には、ピッキングリストの確認を徹底する、作業時間を適切に管理して休憩を取らせる、作業員に対するトレーニングを充実させる、システムの安定性を確保する、作業環境を改善するといった対策が考えられます。このような取り組みにより、数量ミスの発生を抑え、業務の精度を高めることが可能となります。
そんな時に使えるなぜなぜ分析
なぜなぜ分析とは、問題の根本原因を明らかにし、効果的な解決策を導き出すための手法で、特に製造業や物流、サービス業などで広く活用されています。この手法は、日本のトヨタ生産方式で用いられたことを起源とし、継続的な改善を実現するための基本的な考え方の一つとして発展しました。トヨタでは、「問題の根本原因を特定するためには『なぜ?』を5回繰り返せ」と提唱されており、これが現在のなぜなぜ分析の基礎となっています。
なぜなぜ分析の目的は、単に表面的な原因を取り除くことではなく、問題を引き起こした根本的な要因を探り、それを排除することで再発を防ぐことにあります。この手法では、まず解決すべき問題を具体的に定義し、次に「なぜその問題が起きたのか?」を問いかけ、その答えに対して再び「なぜ?」を繰り返していきます。このプロセスを経ることで、問題の背景にある複数の要因を段階的に明らかにすることができます。具体的には、「なぜ出荷ミスが発生したのか?」という問いに対して、「ピッキングリストを確認しなかった」という答えが出た場合、さらに「なぜ確認しなかったのか?」と問い続けることで、例えば「作業員の教育が不十分だった」や「作業環境が整っていなかった」といった根本原因が明らかになります。
この手法を効果的に実施するためには、問題を曖昧にせず、具体的に定義することが重要です。また、客観的なデータに基づいて分析を行い、関係者全員で議論を進めることで、多角的な視点から原因を追究できます。そして、最終的に特定した根本原因に対する解決策を実行し、その効果を評価・改善するというサイクルを繰り返すことで、継続的な改善が可能になります。
なぜなぜ分析は、シンプルな手法でありながら、問題解決能力を高める強力なツールであり、現場の実務だけでなく、プロジェクト管理や業務改善にも応用されています。その実践においては、「なぜ」の問いかけを感情論や責任追及にせず、論理的かつ建設的に進めることが成功の鍵となります。このようになぜなぜ分析を活用することで、組織全体の課題解決力を向上させ、長期的な成長を実現することができます。
なぜなぜ分析例題
ある日の出荷で、顧客Aに送るべき「化粧水A」が、顧客Bに送付されました。
一方、顧客Aには「化粧水B」が送られていました。
なぜなぜ分析の詳細
1. なぜ顧客Aに「化粧水A」ではなく「化粧水B」が送られたのか?
理由: ピッキングの際に、担当者が「化粧水A」の棚ではなく「化粧水B」の棚から商品を取ってしまった。
2. なぜ担当者は「化粧水A」の棚ではなく「化粧水B」の棚から取ったのか?
理由: 棚のラベルが見にくく、「化粧水A」と「化粧水B」が隣り合っており、商品を間違えた。
3. なぜ棚のラベルが見にくく、「化粧水A」と「化粧水B」を間違えたのか?
理由: ラベルには商品のフルネームとバーコードしか記載されておらず、視認性が低かった。また、棚番号の色分けや区別がされていなかった。
4. なぜ視認性の低いラベルが使われていたのか?
理由: 倉庫管理システム(WMS)の導入時に、ラベルのデザインや棚の配置の視認性が検討されなかった。
5. なぜラベルや棚の視認性が検討されなかったのか?
理由: 導入時、ピッキング作業員の意見が反映されず、現場の実際の運用が考慮されなかった。
なぜなぜ分析から導き出す具体的な対策
1. 棚ラベルの改善
商品名を大きく表示し、顧客別または商品カテゴリー別の色分けを実施する(例:「化粧水A」のラベルは青、「化粧水B」のラベルは緑)。
ラベルに「写真」を追加して商品パッケージと一致させる。
2. 棚の配置見直し
よく似た名前やパッケージの商品が隣り合わないように棚の配置を変更。
顧客別の専用棚エリアを作成し、誤ピッキングを減らす。
3. ピッキング作業のサポートツール導入
デジタルピッキングシステムを導入し、バーコードスキャナーで商品を確認してエラーを防ぐ。
作業者が正しい棚から商品を取る際にランプや音で通知するシステムを設置。
4. 作業プロセスの見直し
ピッキング完了後、別の担当者によるダブルチェックをルール化。
チェック時に、商品名・数量・顧客情報を再確認する作業を徹底する。
5. 現場の意見を取り入れる
現場作業員から「誤ピッキングが発生しやすい商品」のリストアップを依頼。
作業員が参加する改善ミーティングを定期的に実施。
改善後の予想効果シナリオ
・新しいラベルと色分けにより、商品識別が一目で可能になる。
・棚の配置変更で類似商品を間違える確率が激減。
・デジタルピッキングシステムにより、誤ピッキングが起きた場合もすぐに警告が出る。
・ダブルチェックの徹底により、出荷ミスが99%以上削減される。
「なぜなぜ分析」とは?と仕組み
根本原因を探るプロセス
「なぜなぜ分析」とは、問題が発生した原因を突き止め、根本的な解決策を見つけるための手法です。誤出荷が発生した場合、単に表面的な原因を追求するのではなく、なぜその原因が発生したのか、さらにその原因は何か、と深掘りしていくことで、根本的な原因を特定することができます。
なぜなぜ分析は、問題解決のための重要なツールとして、様々な分野で活用されています。特に、誤出荷防止においては、原因を徹底的に分析することで、再発防止策を効果的に策定することができます。
1.問題の特定
まず、問題を具体的に特定します。例えば、「商品Aを10個注文したのに、5個しか届かなかった」という問題が発生した場合、問題を「商品Aの数量不足」と特定します。
2.なぜ?を繰り返す
問題が発生した原因を「なぜ?」と問い続け、その原因をさらに深掘りしていきます。
・なぜ商品Aの数量が不足したのか? →ピッキングリストの確認不足
・なぜピッキングリストの確認不足があったのか? → 作業員の集中力低下
・なぜ作業員の集中力低下があったのか? →長時間同じ作業を続けていた
3.根本原因の特定
なぜなぜ分析を繰り返すことで、問題の根本原因にたどり着きます。上記の例では、根本原因は「長時間同じ作業を続けていた」となります。
4.対策の立案
根本原因が特定できたら、その原因を取り除くための対策を立案します。上記の例では、作業時間の見直しや休憩時間の確保などが考えられます。
なぜなぜ分析は、問題解決のための非常に有効な手法ですが、以下の点に注意する必要があります。
・分析の深掘りが重要:表面的な原因にとどまらず、なぜその原因が発生したのかを徹底的に深掘りすることが重要です。
・客観的な視点を持つ:感情的な判断ではなく、客観的な視点で分析を行うことが重要です。
・チームで取り組む:なぜなぜ分析は、チームで取り組むことでより効果的になります。
実践でのポイント
なぜなぜ分析を効果的に実施するためには、いくつかの重要なポイントを押さえる必要があります。まず、問題を具体的に定義することが欠かせません。これにより、分析の目的が明確になり、無駄な議論や混乱を防ぐことができます。また、分析を進める際にはデータに基づくことが重要です。データを活用することで、客観的な根拠をもとにした信頼性の高い対策を立案できます。
さらに、関係者全員で議論を行うこともポイントです。多様な視点を取り入れることで、見落としがちな要因や新たな発見が生まれる可能性があります。そして、対策を実行した後は、その効果を評価し、必要に応じて見直すプロセスを設けることが重要です。これにより、継続的な改善が可能となります。
なぜなぜ分析は、一見すると難しい手法のように感じられるかもしれませんが、基本を押さえれば誰でも実践可能です。日常の問題解決においても、ぜひ積極的に活用してみてください。
自社倉庫で誤出荷を引き起こす主な要因(なぜなぜ分析を使うタイミング)
ピッキング時の確認不足
要因
ピッキング作業中に、ピッキングリストを確認しない、または内容を十分に理解せず作業を進めてしまうことで、誤った商品や数量をピッキングするミスが発生します。類似した商品が近くに配置されている場合や、商品ラベルが分かりにくい場合も、確認不足につながりやすいです。
なぜなぜ分析を使うタイミング
ピッキングミスが繰り返される、または特定の作業員にミスが集中する場合に、原因を深掘りするために「なぜ確認不足が起きるのか?」と問い続けます。例えば、「なぜリストを確認しなかったのか?」から「なぜ視認性の低いラベルが使われているのか?」と掘り下げます。
梱包時のチェック漏れ
要因
梱包作業で、商品が適切な状態で梱包されているか、注文内容と梱包内容が一致しているかを確認する工程が不十分だと、誤出荷につながります。特に、複数の商品を一度に梱包する場合、確認不足が発生しやすくなります。
なぜなぜ分析を使うタイミング
商品と注文内容が一致していないケースが発生した場合や、破損品が顧客に届いた場合に、「なぜチェックが漏れたのか?」を分析します。例えば、「なぜチェック工程が十分でなかったのか?」から始めて、「なぜ作業員が急いで作業していたのか?」と掘り下げます。
出荷前の最終確認不足
要因
出荷時に、伝票や送り状と実際に梱包された商品が一致しているかの最終確認を怠ることで、誤出荷が発生します。特に、繁忙期や作業が急がれる状況では、確認工程が省略されることがあります。
なぜなぜ分析を使うタイミング
誤出荷が顧客からのクレームや返品として報告された場合に、「なぜ最終確認が行われなかったのか?」を深掘りします。例えば、「なぜ作業工程に余裕がなかったのか?」や「なぜ確認工程の重要性が認識されていなかったのか?」と掘り下げることで、根本的な原因を特定します。
なぜなぜ分析を活用した誤出荷防止策
業務フローの見直し
なぜなぜ分析の結果、誤出荷の原因が特定できたら、次はその原因を取り除くための対策を立案する必要があります。誤出荷防止対策として、まず考えられるのは、業務フローの見直しです。
業務フローを見直すことで、作業の効率化を図り、誤出荷が発生しにくい環境を作ることができます。例えば、ピッキング作業の工程を見直し、ピッキングリストの確認を複数回行うようにしたり、梱包作業の工程を見直し、梱包前に商品が破損していないかを確認する工程を追加したりすることができます。
業務フローの見直しを行う際には、以下の点を考慮することが重要です。
業務フローの見直しを行う際には、いくつかの重要な点を考慮する必要があります。まず、作業の標準化を図ることが挙げられます。これにより、作業員のスキルや経験の差によるミスを最小限に抑えることが可能となります。次に、チェックポイントの増設も有効です。これにより、作業過程でのミスを早期に発見し、問題が大きくなる前に対処することができます。
さらに、作業の簡素化を行うことも見直しのポイントです。作業手順を簡素化することで、作業員の負担を軽減するとともに、ミスの発生率を低減できます。また、関係者間での情報共有を強化することも重要です。これにより、誤解や認識のズレを防ぎ、業務全体がスムーズに進行する環境を構築できます。
これらの要素を取り入れることで、業務フローの効率化と正確性の向上が期待できます。
まとめ:なぜなぜ分析で誤出荷ゼロを目指す
効果的な分析と行動が鍵
誤出荷は、企業にとって深刻な問題となる可能性があります。顧客満足度の低下やブランドイメージの悪化、さらには売上機会の損失など、様々な悪影響を及ぼす可能性があります。
誤出荷を防止するためには、なぜなぜ分析を活用し、根本原因を突き止め、適切な対策を講じることが重要です。なぜなぜ分析は、表面的な原因にとどまらず、問題の根本原因を特定することで、効果的な対策を立てることができるため、誤出荷防止に非常に有効な手法です。
チームでの取り組みが成功を呼ぶ
誤出荷防止は、一人の担当者だけで取り組むのではなく、組織全体で取り組むことが重要です。なぜなぜ分析をチームで実施することで、様々な視点から問題を分析することができます。また、チームで対策を立案することで、より効果的な対策を立てることができます。
誤出荷防止は、企業にとって重要な課題です。なぜなぜ分析を活用し、チームで取り組むことで、誤出荷ゼロを目指しましょう。
誤出荷が頻発するなら、誤出荷ゼロを達成し続けている物流倉庫会社、株式会社三協へご相談を
誤出荷が頻発してお困りの場合、誤出荷ゼロを達成し続ける物流品質の高い株式会社三協にご相談ください。同社は、独自開発の倉庫管理システム(WMS)を活用し、全商品の在庫を一元管理することで、誤出荷や在庫差異を徹底的に防止し、物流の効率化を実現しています。また、1968年の創業以来、現場主義を徹底し、創意工夫を重ねた物流改善ノウハウを蓄積しており、結果報酬型のサービスを提供することでコスト削減と品質向上を両立しています。誤出荷をはじめとする物流課題を解決したい場合は、物流改善代行サービスを通じて多数の実績を誇る株式会社三協をご検討ください。