誤出荷を防ぐための対策と解決するためのフレームワーク10選
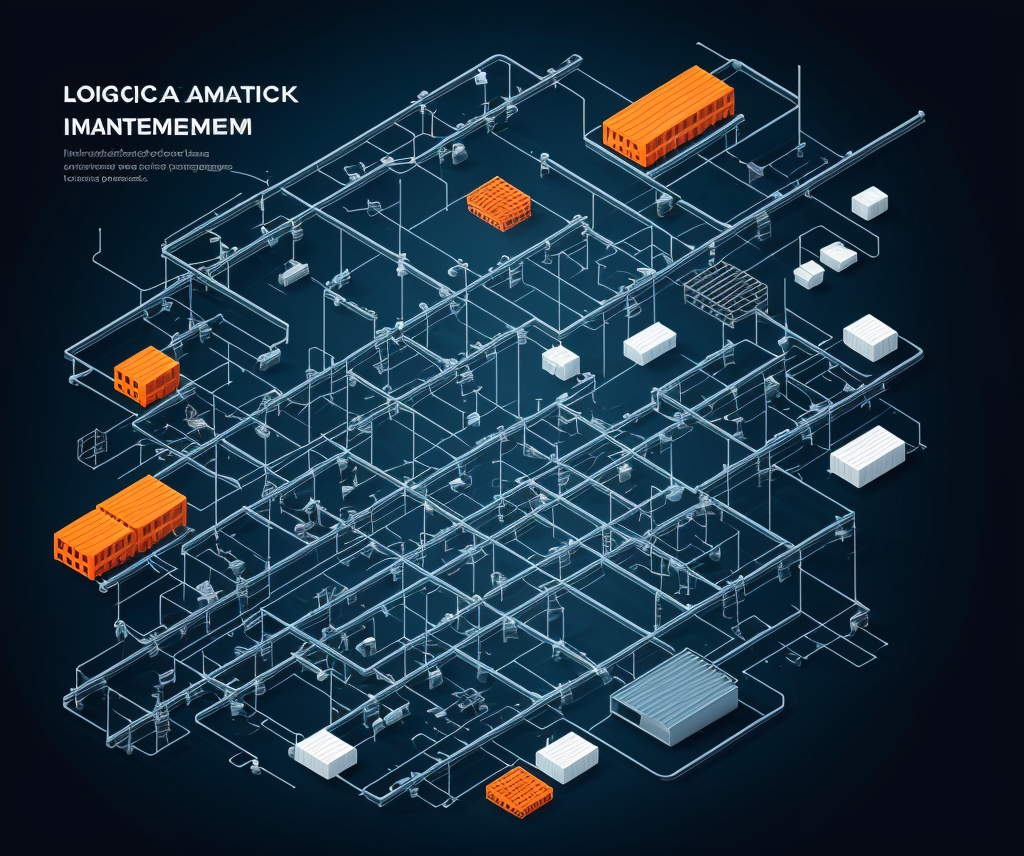
物流における誤出荷は企業の信頼を損なう重大な問題です。この記事では、誤出荷を防ぐための効果的な対策と、実務に役立つフレームワークを紹介します。
誤出荷とは?その影響と原因
誤出荷がもたらす影響
誤出荷は、企業にとって深刻な問題です。顧客への信頼を失墜させ、多大なコスト負担を強いる可能性があります。誤出荷によって生じる具体的な影響を以下にまとめます。
・顧客満足度の低下:誤った商品が届いた場合、顧客は大きな不満を抱き、企業に対する信頼を失う可能性があります。これは、リピート購入率の低下やネガティブな口コミの拡散につながり、企業のブランドイメージを損なう可能性があります。
・売上機会の損失:誤出荷によって顧客が商品を受け取れなかった場合、企業は売上機会を失うことになります。特に、受注生産品や希少価値の高い商品の場合、顧客の注文を逃すことは大きな損失となります。
・コストの増大:誤出荷が発生すると、商品の再出荷や返品処理、顧客対応など、追加の費用が発生します。また、誤出荷によって発生したトラブルの解決には、人的資源や時間的なコストも必要となります。
・競争力低下:誤出荷は、企業の競争力を低下させる要因となります。顧客満足度が低下し、コストが増加することで、企業は競合他社に対して不利な立場に立たされる可能性があります。
・ブランドイメージの悪化:誤出荷は、企業のブランドイメージを悪化させる可能性があります。顧客からのクレームやメディア報道によって、企業の評判が傷つき、顧客からの信頼を失う可能性があります。
誤出荷は、企業にとって様々な悪影響をもたらすため、徹底的な対策を講じる必要があります。
誤出荷の主な原因
誤出荷が発生する原因は様々ですが、主な原因として、人的ミスとシステムエラーが挙げられます。
・人的ミス:人間の注意力や判断力の限界によって発生するミスです。以下のような状況が考えられます。
・ 注文情報の入力ミス:商品コードや数量、配送先住所などの入力ミスは、誤出荷の最も一般的な原因です。
・ピッキングミス:倉庫内での商品ピッキング時に、間違った商品をピックアップしてしまうミスです。
・パッキングミス:商品を梱包する際に、間違った商品を入れたり、必要な付属品を漏らしたりするミスです。
・ 発送ミス:出荷伝票の記載ミスや、配送先住所の誤入力によって、商品が間違った場所に発送されてしまうミスです。
・システムエラー:システムの不具合や設定ミスによって発生するミスです。以下のような状況が考えられます。
・ 在庫管理システムの誤動作:在庫管理システムのデータが誤っている場合、誤出荷が発生する可能性があります。
・注文処理システムの不具合:注文処理システムに不具合が発生した場合、注文内容が正しく処理されず、誤出荷が発生する可能性があります。
・ 配送システムのエラー:配送システムにエラーが発生した場合、商品が予定通りに配送されず、誤出荷が発生する可能性があります。
誤出荷の原因を特定し、適切な対策を講じることで、誤出荷を防止することができます。
誤出荷防止の基本対策
インベントリの精度向上
正確な在庫管理は、誤出荷防止の基礎となります。在庫管理システムの導入によって、リアルタイムで在庫状況を把握できるため、在庫データの正確性を高め、誤出荷のリスクを軽減できます。また、定期的な棚卸を実施することで、システム上の在庫データと実際の在庫状況を照合し、誤差を修正することが可能です。さらに、在庫管理のルールを標準化することで、担当者間の認識のずれを防ぎ、誤出荷のリスクを低減できます。加えて、在庫回転率を改善することで、在庫の陳腐化を防ぎ、誤出荷のリスクを軽減できます。
在庫管理の精度を高めることで、誤出荷を防止し、顧客満足度の向上に貢献できます。
パッキングプロセスの最適化
パッキングプロセスは、誤出荷が発生しやすい工程の一つです。そのため、作業の標準化やチェック体制の強化を通じて、パッキングミスを最小限に抑えることが重要です。
パッキング作業の標準化により、作業手順を明確化し、担当者間の認識のずれを防ぐことでミスを減らすことができます。一貫性のある作業フローが確立されれば、誰が担当しても安定した品質を保つことが可能です。
また、チェックリストの導入を行い、パッキング作業前に商品や付属品が揃っているか確認することで、出荷内容の誤りを防ぎます。チェックリストは視覚的にわかりやすく、作業者にとって確認しやすい形式で用意することが効果的です。
パッキングエリアの改善も重要な要素です。エリアのレイアウトを見直し、作業スペースを十分に確保することで、作業者が効率的かつ正確に作業を進められる環境を整えます。整理された作業エリアは、ミスの防止だけでなく作業者のストレス軽減にも寄与します。
加えて、パッキング機器の導入により、作業効率の向上と品質の安定を図ることが可能です。自動梱包機やラベル印刷機などの設備を導入することで、作業者の負担を軽減し、人為的なミスを大幅に減少させることができます。
これらの施策を通じてパッキングプロセスを最適化することで、誤出荷を防止し、顧客への商品配送の精度を高め、顧客満足度の向上に貢献することができます。
チェックリストの導入
チェックリストの導入は、誤出荷防止に非常に効果的な手段であり、作業工程ごとに専用のチェックリストを作成し活用することで、人的ミスを大幅に減らすことができます。たとえば、注文内容や配送先住所を確認する「注文確認チェックリスト」、ピッキングした商品と注文内容が一致しているかを確認する「ピッキングチェックリスト」、梱包時に商品や付属品、梱包材が揃っているかを確認する「パッキングチェックリスト」、出荷伝票や配送方法を確認する「発送確認チェックリスト」などがあり、それぞれの工程で確認作業を徹底することで、業務精度を向上させ、担当者の負担を軽減しながら顧客満足度の向上にもつなげることが可能です。
誤出荷防止に役立つフレームワーク10選
1、ECRS(エリミネーション・コンバイネーション・リアレンジ・シンプルファイ)
ECRSは、物流プロセスを改善するためのフレームワークです。ECRSの4つのステップを踏むことで、誤出荷の原因となる無駄を排除し、効率的な物流プロセスを構築することができます。
・エリミネーション(排除):不要な作業や工程を徹底的に排除します。例えば、重複するチェック作業や、不要な書類作成などを廃止することで、作業の効率化を図ることができます。
・コンバイネーション(結合):複数の作業を組み合わせることで、作業の効率化を図ります。例えば、ピッキングとパッキングを同時に行うことで、作業時間を短縮することができます。
・リアレンジ(配置換え):作業の順番や配置を工夫することで、作業の効率化を図ります。例えば、頻繁に使用する商品を、取り出しやすい場所に配置することで、ピッキング時間を短縮することができます。
・シンプルファイ(簡素化):作業を簡素化することで、作業の効率化を図ります。例えば、複雑な手順を簡略化したり、わかりやすいマニュアルを作成したりすることで、作業ミスを減らすことができます。
ECRSを活用することで、物流プロセス全体を見直し、誤出荷の原因となる無駄を排除することができます。
2、PDCAサイクル(Plan-Do-Check-Act)
PDCAサイクルは、業務プロセスの継続的な改善を促進するための基本的なフレームワークです。まず「計画(Plan)」段階では、問題点を洗い出し、目標設定や改善策の策定を行います。次に「実行(Do)」段階で計画した改善策を実施します。その後、「確認(Check)」段階で実施した結果を評価し、目標達成度や問題点を分析します。最後に「改善(Act)」段階で評価結果に基づき、さらなる改善策を検討し、次のサイクルに反映させます。このプロセスを繰り返すことで、組織は業務の効率性と品質を継続的に向上させることができます。誤出荷防止においては、出荷プロセス全体をPDCAサイクルで管理し、ミスの原因を特定し、適切な対策を講じることで、再発防止につなげることが可能です。
3、5S活動
5S活動は、職場環境を整備し、効率的で安全な作業環境を実現するための手法です。「整理」では必要なものと不要なものを区別し、不要なものを排除します。「整頓」では必要なものを取り出しやすく配置し、見つけやすくします。「清掃」は日常的に職場を清掃し、機器や設備の異常を早期に発見します。「清潔」は整理・整頓・清掃の状態を維持し、標準化します。「しつけ」は決められたルールや手順を守る習慣を育てます。出荷業務において5S活動を徹底することで、商品や書類の紛失や混在を防ぎ、誤出荷のリスクを大幅に減少させることができます。また、清潔で整然とした職場は従業員の士気向上にも寄与します。
4、なぜなぜ分析(根本原因分析)
なぜなぜ分析は、問題の表面的な原因だけでなく、根本的な原因を明らかにするための手法です。一つの問題について「なぜ」を繰り返し問いかけ、深層にある真の原因にたどり着きます。一般的には5回程度「なぜ」を繰り返します。例えば、誤出荷が起きた場合、最初の「なぜ」で「商品を取り違えたから」と答えます。次の「なぜ」で「類似した商品が隣り合わせに置かれていたから」と深掘りします。このプロセスを繰り返すことで、倉庫レイアウトの問題や教育不足など、根本的な課題を特定できます。これにより、再発防止策を的確に策定し、同様のミスを防ぐことが可能となります。
5、FMEA(Failure Mode and Effects Analysis)
FMEAは、製品やプロセスにおける潜在的な故障モードとその影響を分析し、予防策を講じる手法です。具体的には、各工程で起こり得る失敗の種類、原因、影響をリストアップし、それぞれの発生頻度、深刻度、検出可能性を評価します。その評価に基づき、リスクの高い項目を特定し、優先的に対策を実施します。出荷業務では、ピッキングミスやラベル貼付ミス、配送先間違いなどの潜在的な問題を洗い出し、それぞれに対する予防策を検討します。FMEAを活用することで、誤出荷のリスクを事前に把握し、プロセス全体の信頼性を高めることができます。
6、シックスシグマ(Six Sigma)
シックスシグマは、データと統計手法に基づき、プロセスのばらつきを減らし品質を向上させる手法です。DMAIC(Define、Measure、Analyze、Improve、Control)の5つのステップで構成されます。まず「定義(Define)」で問題を明確化し、「測定(Measure)」で現状のパフォーマンスを測定します。「分析(Analyze)」でデータを解析し、問題の原因を特定します。「改善(Improve)」では、原因に対する解決策を実施し、「管理(Control)」で改善策の効果を維持します。誤出荷問題に対しては、シックスシグマを適用することで、具体的なデータに基づいた改善策を策定し、品質の安定化と顧客満足度の向上を図ることができます。
7、リーン生産方式(Lean Manufacturing)
リーン生産方式は、無駄を徹底的に排除し、価値を最大化するための手法です。無駄は大きく7つ(過剰生産、待ち時間、運搬、加工そのもの、在庫、動作、不良)に分類されます。出荷業務においては、在庫の最適化、プロセスの流れの改善、作業者の動線の効率化などが重要です。例えば、ピッキング作業での無駄な移動を減らすために商品の配置を最適化したり、不必要な在庫を減らすことで在庫管理の手間を省きます。これにより、プロセス全体の効率が向上し、誤出荷のリスクも低減します。また、従業員の負担軽減にもつながり、生産性と品質の両面で効果を発揮します。
8、標準作業手順(Standard Work)
標準作業手順は、最も効率的で品質の高い作業方法を文書化し、全員が一貫して実行できるようにする手法です。これにより、作業者間のばらつきをなくし、品質と生産性を向上させます。出荷業務では、商品のピッキング方法、検品手順、梱包方法、出荷ラベルの貼付など、各工程でのベストプラクティスを明確にします。標準化された手順は教育・訓練の基礎となり、新人でも短期間で高品質な作業が可能になります。また、手順が明確であるため、問題発生時の原因追及や改善策の策定も容易になります。標準作業手順は、継続的な見直しと更新を行うことで、常に最適な状態を維持できます。
9、TQM(Total Quality Management)
TQMは、全社的な品質管理活動を通じて、組織全体の品質を向上させるフレームワークです。顧客満足を最優先とし、全従業員が品質改善に参加する文化を育成します。具体的な取り組みとして、品質目標の設定、プロセスの管理、教育・訓練、チーム活動などがあります。出荷業務では、誤出荷ゼロを目標に掲げ、各部門が連携して改善活動を行います。例えば、品質サークルを組織し、現場の従業員が自主的に問題解決に取り組む機会を提供します。また、顧客からのフィードバックを積極的に収集し、サービスの改善につなげます。TQMの実践により、組織全体の品質意識が高まり、持続的な成長が期待できます。
10、ポカヨケ(Error Proofing)
ポカヨケは、人為的なミスを未然に防ぐための仕組みや装置を導入する手法です。作業プロセス自体を見直し、ミスが起きにくい、あるいは起きてもすぐに検知できるように設計します。出荷業務では、バーコードスキャンによる商品確認、重量センサーによる検品、自動仕分けシステムの導入などが効果的です。また、物理的なガイドやテンプレートを使用して、誤った手順を防ぐことも可能です。ポカヨケの導入により、作業者の熟練度に関係なく、高い品質を維持できます。これにより、誤出荷のリスクを大幅に減少させ、顧客からの信頼性を向上させることができます。
実務に役立つ誤出荷防止ツール
WMSの活用
WMS(倉庫管理システム)は、在庫や物流業務を効率的かつ正確に管理するための重要なツールです。このシステムは、商品の入出庫、在庫管理、ピッキング、パッキング、出荷までの一連の工程を一元管理します。
WMSを活用することで、リアルタイムでの在庫状況の把握が可能となり、商品の誤出荷や在庫不足といった問題を未然に防ぐことができます。また、ピッキングリストや作業指示をデジタル化し、作業者に正確な情報を提供することで、ピッキングやパッキングミスの発生を抑えることができます。さらに、業務データを蓄積して分析することで、改善すべきポイントを明確化し、物流業務全体の効率化を図ることも可能です。
WMSは特に多品種少量出荷を扱う企業や、業務量の多い倉庫でその効果を発揮し、誤出荷防止と業務品質の向上に寄与します。
バーコード
バーコードシステムは、物流や倉庫業務において誤出荷防止の要となるツールです。商品のピッキング、パッキング、出荷時にバーコードをスキャンすることで、注文内容との照合が簡単かつ正確に行えます。特に、システムと連動することで、スキャンした商品情報がリアルタイムで更新され、在庫データとの不一致や誤配送のリスクを大幅に低減します。また、バーコードシステムは作業効率を向上させる点でも有用で、従来の目視確認に比べて作業時間が短縮されるため、作業者の負担軽減にもつながります。さらに、誤出荷が発生した際の原因追及も容易になり、業務改善のスピードが上がる点も魅力です。バーコードは比較的低コストで導入可能なため、規模を問わず多くの企業で活用されており、物流の信頼性向上に大きく貢献します。
保管什器
保管什器(ラックや棚などの収納設備)は、倉庫内での商品保管を効率化し、誤出荷防止に寄与する重要なツールです。適切な保管什器を導入することで、商品の種類ごとに明確な区分けが可能となり、ピッキングミスや取り違えを防ぐことができます。たとえば、商品サイズや形状に応じた棚の配置や、頻出商品を取り出しやすい場所に配置することで、作業効率が向上し、ヒューマンエラーを最小限に抑えることができます。また、棚にラベルやカラーコードを付けることで視覚的に商品を特定しやすくなり、さらなる精度向上が期待できます。さらに、保管什器を活用して在庫を整然と管理することで、定期的な棚卸作業もスムーズに行えるようになります。保管什器の適切な導入は、作業環境の整備と効率化を同時に実現し、誤出荷防止の基盤を築くうえで欠かせない施策です。
まとめ
誤出荷は、企業にとって深刻な問題です。顧客満足度の低下、コストの増大、ブランドイメージの悪化など、様々な悪影響をもたらします。誤出荷を防止するためには、基本対策の徹底とフレームワークの活用が不可欠です。
誤出荷防止は、企業にとって重要な課題です。これらの対策を講じることで、物流業務の質を向上させ、顧客満足度を高めることができます。
株式会社三協は、誤出荷ゼロを目指した物流業務のプロフェッショナルです。独自のノウハウと徹底した管理体制により、物流業務の品質向上を実現しています。また、誤出荷防止だけでなく、倉庫内のレイアウト改善や作業効率化、コスト削減まで幅広い物流改善代行サービスも提供しています。物流における課題を抱えている企業様に寄り添い、現状分析から最適な改善策のご提案から実作業まで一貫してサポートいたします。物流の品質向上や業務効率化をお考えなら、ぜひ三協にご相談ください。業務改善を通じて、お客様の信頼を勝ち取る物流環境をお届けします。