物流なぜなぜ分析|ヒューマンエラーを防ぐための実践方法
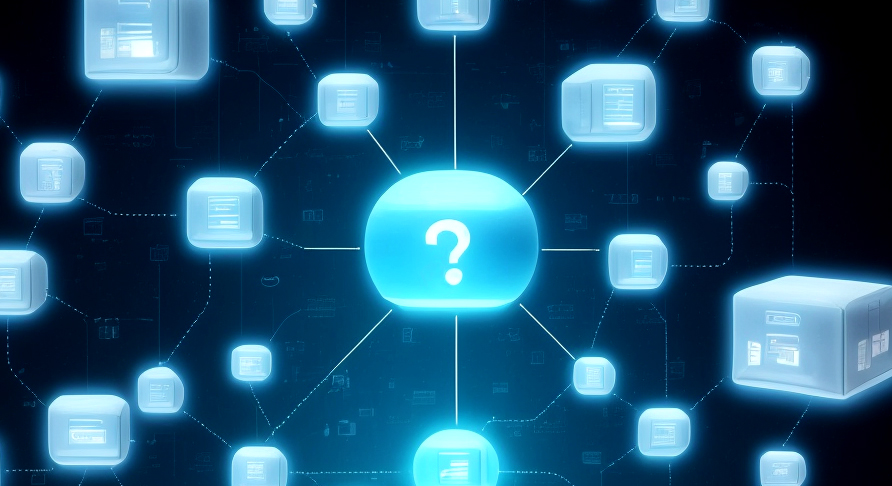
物流現場で頻発するヒューマンエラーを防ぐためには、なぜなぜ分析が重要です。この記事では、物流業界でのなぜなぜ分析の活用方法やヒューマンエラーの防止策について詳しく解説します。
なぜなぜ分析とは何か
ヒューマンエラーを防ぐためのなぜなぜ分析の目的
物流現場でヒューマンエラーを防ぐためのなぜなぜ分析の目的を解説します。なぜなぜ分析は、問題発生の原因を突き止め、根本的な対策を講じるための強力なツールです。
まず、起きてしまった問題に対して「なぜ?」と原因を考え、導き出した答えに対してさらに「なぜ?」と問いかけをし、原因を深堀していきます。「なぜ?」を5回繰り返すことにより表面的な原因にとどまらず、問題の根本原因を探り、再発防止に効果的な対策を導き出すことを目的としています。
物流現場では、人為的なミスによる誤出荷や納期遅延といったヒューマンエラーが頻繁に発生します。これらのエラーは、顧客満足度を低下させ、企業の信用失墜にも繋がるため、徹底的な対策が必要です。
分析の重要性と導入効果
物流業界は、多様な業務プロセスと人材、そして複雑なサプライチェーンによって構成されています。そのため、ヒューマンエラーが発生しやすい環境と言えるでしょう。
なぜなぜ分析を導入することで、以下の効果が期待できます。
1.ヒューマンエラーの根本原因究明 : 表面的な原因にとどまらず、問題の根本原因を特定することで、効果的な対策を講じることができます。
2. 再発防止策の策定 : 根本原因を特定することで、再発防止策を効果的に策定し、同様のエラーの発生を抑制できます。
3. 業務プロセスの改善 : 問題点の洗い出しと対策によって、業務プロセス全体を見直し、効率化を図ることができます。
4. 従業員の意識改革 : なぜなぜ分析を通して、従業員は自身の業務における責任感と問題解決能力を高めることができます。
5. 安全性の向上 : ヒューマンエラーによる事故や怪我を防止し、安全な作業環境を実現できます。
なぜなぜ分析は、物流現場における安全性の向上、業務効率の改善、そして顧客満足度の向上に大きく貢献すると言えるでしょう。
物流現場におけるなぜなぜ分析の実践
実際の問題発生時に活用する手順
問題が発生した際にどのようになぜなぜ分析を行うのか、その手順を以下に解説します。
1.問題の特定 :問題が発生した日時、場所、状況、影響範囲などを記録します。
2. 原因の特定 : なぜその問題が発生したのか、5W1H(いつ、どこで、誰が、何を、なぜ、どのように)を基に詳細に調査します。
3.根本原因の特定 : なぜその原因が発生したのか、なぜその状況になったのかを繰り返し追及することで、根本原因にたどり着きます。
4.対策の立案 : 対策は、根本原因に焦点を当て、効果的で現実的なものにする必要があります。
5.対策の実施 : 対策の実施にあたっては、責任者を決め、スケジュールを設定し、進捗状況を定期的に確認します。
6. 効果の検証 : 対策が効果を発揮しているかどうか、定量的な指標を用いて評価します。
7. 改善 : 必要に応じて、対策を再検討し、より効果的なものへと進化させていきます。
なぜなぜ分析は、問題解決のためのサイクルを回すことで、継続的な改善を促進します。
ヒューマンエラー防止のための具体策
ヒューマンエラーを防ぐために、物流現場で実施すべき具体策について示します。なぜなぜ分析を通して、ヒューマンエラーの原因が特定できたら、次はその原因に対する具体的な対策を講じる必要があります。以下に、物流現場でよく見られるヒューマンエラーとその対策例をいくつか紹介します。
1. 誤出荷 : 誤出荷は、物流現場で最も多く発生するヒューマンエラーの一つです。
対策例
・出荷前の検品体制の強化 : 複数人による検品、バーコードスキャナーの導入、ダブルチェック体制の構築など
・ 出荷指示書や伝票の確認徹底 : 誤った指示書や伝票による出荷を防ぐため、担当者による確認を徹底する
・出荷エリアの整理整頓 : 出荷エリアの整理整頓を行い、誤出荷を防ぐ
2. 納期遅延 : 納期遅延は、顧客満足度を大きく損なう要因となります。
対策例
・作業工程の標準化 : 作業工程を標準化し、作業時間のばらつきを減らす
・作業スケジュールの見直し : 作業スケジュールを見直し、余裕を持った計画を立てる
・搬送ルートの最適化 : 搬送ルートを最適化し、搬送時間を短縮する
3. 破損 : 商品の破損は、顧客への損失だけでなく、企業の評判にも悪影響を与えます。
対策例
・梱包方法の改善 : 商品の特性に合わせた適切な梱包方法を採用する
・搬送時の取り扱い注意 : 搬送時の取り扱い方を徹底し、破損を防ぐ
・搬送車両の点検: : 搬送車両の定期的な点検を行い、安全性を確保する
4. 紛失 : 商品の紛失は、顧客への損失だけでなく、企業の信用失墜にも繋がる可能性があります。
対策例
・在庫管理システムの導入 : 在庫管理システムを導入し、商品の入出庫状況を正確に把握する
・荷物の追跡システムの導入 : 荷物の追跡システムを導入し、荷物の所在を常に把握できるようにする
・倉庫内での整理整頓 : 倉庫内を整理整頓し、荷物の紛失を防ぐ
これらの対策は、あくまでも一例です。物流現場の状況に合わせて、適切な対策を検討する必要があります。
効果的な実行と検証方法
なぜなぜ分析を実施した後の効果を検証し、さらなる改善に繋げる方法を紹介します。なぜなぜ分析を実施しただけでは、効果は期待できません。分析結果に基づいて対策を講じ、その効果を検証し、さらに改善を続けることが重要です。効果的な検証方法としては、以下の方法が挙げられます。
1. 定量的な指標を用いた評価 : 誤出荷率、納期遅延率、破損率、紛失率などの定量的な指標を用いて、対策の効果を評価します。
2. アンケート調査 : 従業員や顧客へのアンケート調査を実施し、対策の効果に関する意見や感想を収集します。
3. ヒアリング : 現場担当者へのヒアリングを実施し、対策の実施状況や効果に関する情報を収集します。
4. データ分析 : 過去のデータと対策実施後のデータを比較分析することで、対策の効果を検証します。
検証結果に基づいて、対策を改善し、より効果的なものへと進化させていくことが重要です。
なぜなぜ分析でヒューマンエラーを防ぐためのコツ
現場の実情を踏まえた分析のポイント
なぜなぜ分析は、現場の状況を深く理解することが重要です。現場の状況を把握せずに、机上の空論で分析を進めても、効果的な対策を講じることができません。
現場の状況を踏まえた分析のポイントは以下の通りです。
1. 意見を積極的に聞き取る
現場の担当者は、日々の業務の中で、問題点や改善点に気づいていることが多いです。
2. 状況を実際に観察する
現場に足を運び、実際に作業の様子を直接確認します。
3. データを集める
データとは、作業時間、不良発生件数、在庫状況、顧客からのクレームなどです。
4. 課題を共有する
全員が問題意識を共有することで、より効果的な対策を講じることができます。
現場の状況を深く理解することで、適切な分析を実施することができます。
多角的な視点での検討方法
問題を多角的に分析するために必要な視点と方法について説明します。なぜなぜ分析では、問題を単一の視点からではなく、多角的な視点から分析することが重要です。多角的な視点から分析することで、より深く問題を理解し、効果的な対策を講じることができます。
また、ヒューマンエラーには「動作、記憶、認知、判断、環境」と原因を5つに分類できます。分類を分けすることで改善すべきことが明確になります。
1. 人 : 動作のエラー、判断のエラー
人為的なミスが原因となっている可能性を検討します。作業者のスキル不足、疲労、集中力の低下、コミュニケーション不足などが考えられます。
2. 物 : 環境のエラー
物流機器や設備が原因となっている可能性を検討します。機器の故障、老朽化、使い勝手の悪さなどが考えられます。
3. 方法 : 認知のエラー、判断のエラー
作業方法や手順が原因となっている可能性を検討します。作業手順の複雑さ、非効率性、標準化されていない作業などが考えられます。
4. 作業条件 : 環境のエラー
作業環境が原因となっている可能性を検討します。照明不足、騒音、温度湿度、作業スペースの狭さなどが考えられます。
5. システム : 記憶のエラー、認知のエラー
情報システムが原因となっている可能性を検討します。システムの誤動作、データ入力ミス、システムの使いにくさなどが考えられます。
6. 操作 : 動作のエラー
作業者の操作ミスが原因となっている可能性を検討します。例えば、荷物の持ち方が誤っている、機器のボタンを押し間違える、操作のタイミングがずれるなどのケースが考えられます。
これらの視点から問題を正確に分析することで、より深く問題を理解し、効果的な対策を講じることができます。
実例!なぜなぜ分析を用いた誤出荷防止策
物流倉庫で誤出荷が起きた場合の活用例
物流倉庫では、商品の保管、ピッキング、梱包、出荷など、様々な業務が行われています。これらの業務において、ヒューマンエラーが発生すると、誤出荷、納期遅延、破損、紛失などの問題が発生する可能性があります。
例えば、誤出荷が発生した場合、なぜなぜ分析を通して、以下の原因が考えられます。
・ピッキングミス : 商品を間違えてピッキングしてしまった。
・梱包ミス : 商品を間違えて梱包してしまった。
・伝票ミス : 伝票に記載された商品情報が間違っていた。
・システムエラー : 在庫管理システムに誤りが発生した。
これらの原因を突き止め、対策を講じることで、誤出荷を防止することができます。
誤出荷防止の為の業務フローの見直し
なぜなぜ分析を通して、誤出荷の原因が特定できたら、次は業務フローの見直しを行います。業務フローを見直すことで、誤出荷が発生しにくい仕組みを作ることができます。
1.ピッキング工程の改善
・バーコードスキャナーの導入 : バーコードスキャナーを導入する
・ピッキングリストの改善 : ピッキングリストを見やすく、わかりやすく改善する
・ピッキングエリアの整理整頓:ピッキングエリアを整理整頓する
2. 梱包工程の改善
・梱包作業の標準化 : 梱包作業を標準化する
・梱包資材の管理 : 梱包資材を適切に管理する
・梱包前の検品体制 : 検品体制を強化する
3. 出荷指示書の確認
・ダブルチェック体制 : 複数人で出荷指示書を確認する
・出荷指示書のフォーマット : 出荷指示書のフォーマットを見やすく、わかりやすく改善する
これらの改善策を導入することで、誤出荷を大幅に減らすことができます。
システム導入による改善策
なぜなぜ分析を通して、誤出荷の原因がシステムエラーであることが判明した場合、システムの改善が必要となります。システムの改善には、以下の方法が考えられます。
1.在庫管理システムのアップデート: アップデートやバグ修正を行う
2. 在庫管理システムの最適化 : 適切な設定に調整し、システムの精度を向上させる
3. 出荷確認プロセスの強化 : 在庫管理システムと連携した出荷確認プロセスを追加し、二重チェックなどが行えるようにする
4. スタッフへのトレーニング : システム操作に不慣れなスタッフがいる場合、操作方法のトレーニングを実施する
このように既存システムの改善や現状に合わせた対策を提案することで、より現実的な対応策になります。
まとめ
物流現場でのヒューマンエラー防止に向けた「なぜなぜ分析」の重要性と具体的な活用法を解説しました。 エラーを正しく分析していくことで根本原因が特定でき、再発防止策を講じることができます。 ヒューマンエラーが無くなれば、業務効率や安全性の向上、顧客満足度の改善につながることが期待でき、企業の利益にも貢献できるでしょう。