ピッキングスピードは3倍。 ミスしたくても出来ない仕組みに大満足
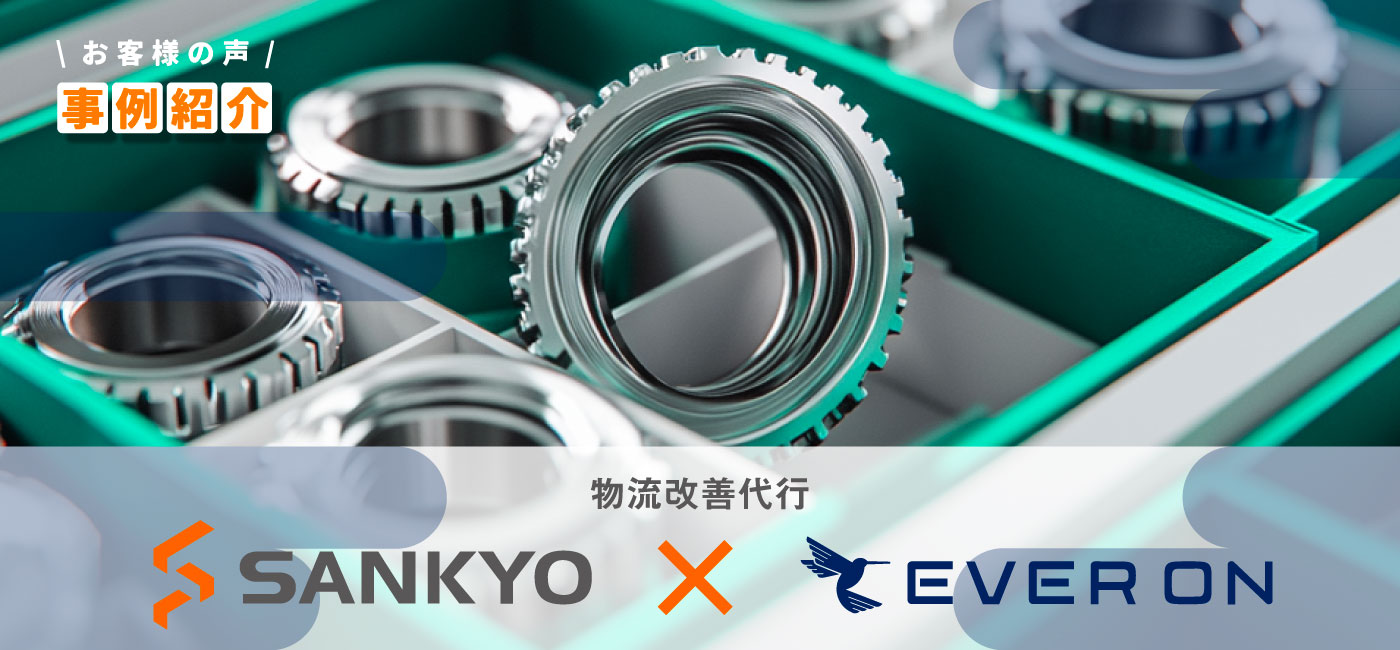
63年前の在庫も揃える。“感動在庫”が我々の使命
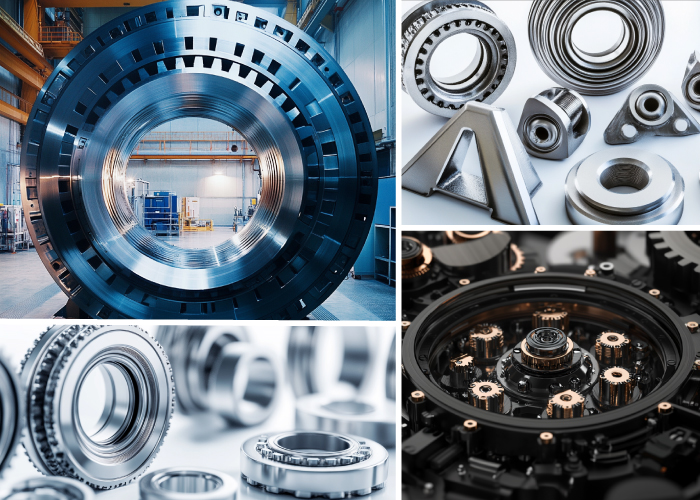
当社は昭和12年、軸受(ベアリング)販売店として創業しました。以来、長い歴史の中で培った専門知識と顧客からの厚い信頼を基盤に、成長を続けてきました。現在は、大阪本社を中心に国内5拠点を構え、さらに海外拠点も展開することで、グローバルにベアリング事業を展開しています。
製品ラインナップはボールベアリングやローラーベアリングなどの一般的なベアリングにとどまらず、産業ロボットや医療分野などの特殊用途製品、最先端技術を持つ海外メーカーの希少なアイテムまで多岐にわたり、多様化するニーズに対応する体制を整えています。
当社の象徴ともいえる取り組みが、”感動在庫”です。これは、廃番となった機材の部品も保有し続けることで、いつどのような状況でもお客様の期待に応えるという当社の使命を具現化したものです。中には、63年前に製造されたアイテムも含まれており、こうした在庫が多くのお客様にとって“最後の砦”となっています。
この徹底した在庫管理によって、急な機材トラブルや部品供給不足といった不測の事態にも迅速に対応し、安心と信頼をお届けすることが可能です。
しかし、この大量在庫を保有する戦略は、一方で管理の難しさという課題を抱えていました。アイテム数の増加とともに在庫管理が煩雑化する中で、基幹システムの制約、アナログ管理の限界、5Sの不徹底が絡み合い、現場では次のような深刻な課題が噴出していました。
(1)出荷ミスや在庫差異の頻発
(2)作業効率(入出荷スピードやピッキング効率)の悪化
(3)未出荷・出荷遅延や現場スタッフの業務負担の増大
さらに、在庫情報の整備不足は現場だけでなく営業活動にも影響を及ぼしていました。顧客からの「在庫があるか?」という問い合わせに即答できず、商機を逃すこともありました。こうした状況は、現場スタッフや営業チーム全体にも大きなストレスをもたらしていました。
こうした状況の中、金融機関からの紹介で三協さんと出会いました。
正直にお話すると、
「当社の内情を知らない第三者に物流改善なんてできるのか?」
「デジタル化をしたら、臨機応変なオペレーションができなくなるのでは?」
という不安がものすごくありました。
しかし、ZOOMなどのWEBの打ち合わせではなく、対面で何度も何度も膝を突き合わせてお話を聞いていくうちに、以下の3点から三協さんに仕事を依頼しようと決めました。
- (1)徹底された管理体制と柔軟な対応力
三協さんの倉庫を実際に見学させていただいた際、物流のプロフェッショナルとして徹底された管理体制や効率的なオペレーションを目の当たりにしました。特に、職能管理表で全スタッフを定量的に管理するとともに、作業の進捗状況(ピッキングや検品の進捗)に応じて、人員配置がリアルタイムで調整される様子が非常に印象的でした。またデジタル管理が徹底されているにもかかわらず、イレギュラーな状況に応じた柔軟な対応(バーコードが一部の商材で付いていない、特定の出荷先を優先的に出荷する等)がミスなく実現できていることにも深い感銘を受けました
- (2)物流改善担当者の経験値と洞察力
三協さんの物流改善担当者は、当社の現場に足を運び、複数のスタッフにヒアリングを行っただけで、何年間もずっと一緒に働いてきたようなレベルで当社が抱えている「根深い潜在的な問題(基幹システムの制約、保管スペースの不足、属人化、イレギュラー対応、取引先との関係性)」を具体的に指摘してくれました。その洞察力と分析力には驚かされるばかりで、これは物流現場で長年にわたり積み重ねてきた膨大な経験があるからこそ可能な技だと実感しました。私たちは、ベアリングのことなら、プロフェッショナルとして何でも答える自信がありますが、この人たちはそれが物流なのだと痛感しました。
- (3)豊富な改善実績
三協さんがこれまでに手掛けた物流改善事例を伺う中で、当社と同じ機械部品業界で同様の物流課題を解決された事例が複数あることを知り、具体的な成功のイメージを持つことができました。これにより、当社の課題にも確実に対応していただけるという安心感を得ることができました。
三協さんの物流改善を受けることで、新しい物流フローや倉庫管理システム(WMS)の導入が実現しました。このシステムの導入により、複雑化していた在庫管理業務が劇的に効率化され、現場スタッフの負担が大幅に軽減されました。また、スピーディな在庫情報の提供が可能となったことで、営業活動の迅速化と顧客対応力の向上も達成できています。
今回の取り組みを通じて、当社が掲げる“感動在庫”を支える基盤がさらに強化されました。これからもお客様の期待を超えるサービスと価値を提供し続け、より一層の信頼と満足を届けていきたいと感じています。
【課題1】5時間かけて、たった1個の商品を探す
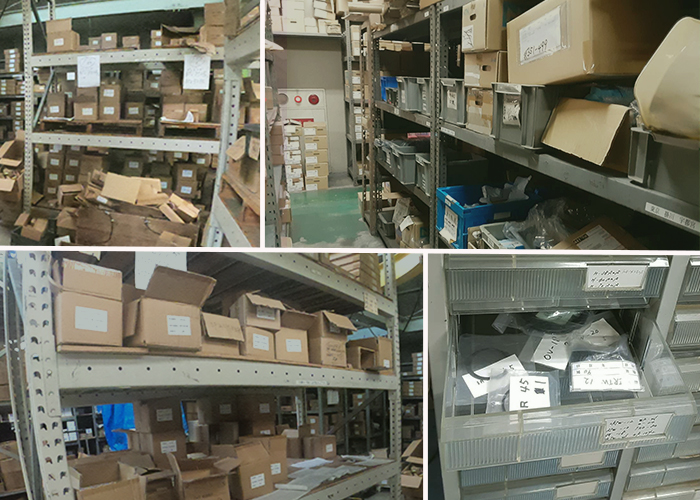
当社は、前述のとおり、主力となる軸受(ベアリング)関連製品に加え、ギヤカップリングなどの伝動装置、空気圧・油圧機器、搬送機器、工場用機械など、非常に幅広い製品を取り扱っております。
その中の、ベアリング関連製品だけでも、ボール・ローラーベアリング、ベアリングユニット、ニードルベアリングなど多様な種類に分かれており、さらにその種類ごとにそれぞれのサイズや形状ごとに品番が枝分かれしています。
さらに、当社のプライベートブランドであるEVNシリーズに加え、仕入商材には日本国内だけでなく海外製品も幅広く取り揃えており、その種類と数は膨大です。この多様性はお客様にとって大きな強みである一方、倉庫内の管理を一層複雑化させる要因にもなっていました。
当社では、倉庫内でのロケーション管理が徹底されておらず、「データでは商品Aがロケーション①にあるはずなのに、見つからない」という問題に直面していました。
その背景には、使用している基幹システムの“制約”がありました。
当社の基幹システムでは、1つの商品に対して登録できるロケーションが最大2か所までと限定されており、以下のような状況が生じるたびに、アナログ管理に頼らざるを得ない状態でした。
(1)入荷時に既存ロケーションが満杯であれば、新たな保管場所が必要になる
(2)先入先出やロット管理のために、新入荷品を別ロケーションへ配置する
(3)棚の耐荷重の制約により、保管場所を分けざるを得ない
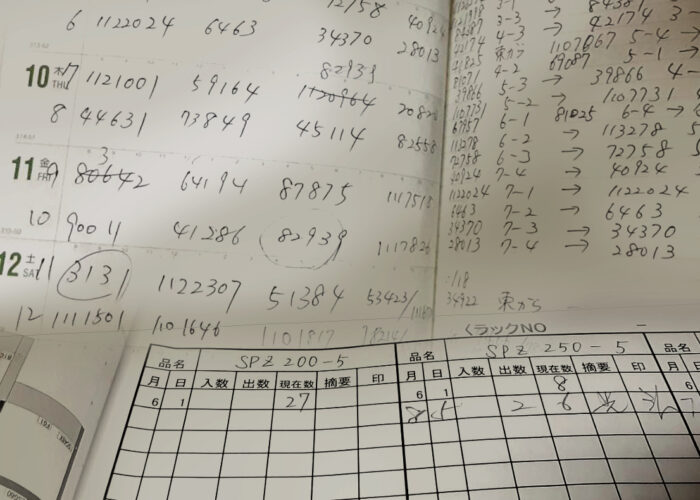
その結果、ロケーション情報の記録が紙や個人のメモに依存し、情報の属人化が深刻化していました。「ロケーション変更」や「一時的に空きスペースへ入庫したという情報」がリアルタイムで共有されず、特定のスタッフしか商品の所在を把握できない状況が常態化していたのです。
また、「予約品の取り置き」や「サンプル品の例外出荷」もアナログ対応に頼っており、記入ミスや更新漏れが発生しても属人化からダブルチェックが適正に機能しないため問題が表面化せず、あるはずのロケーションに商品がないという状態が加速する要因となっていました。
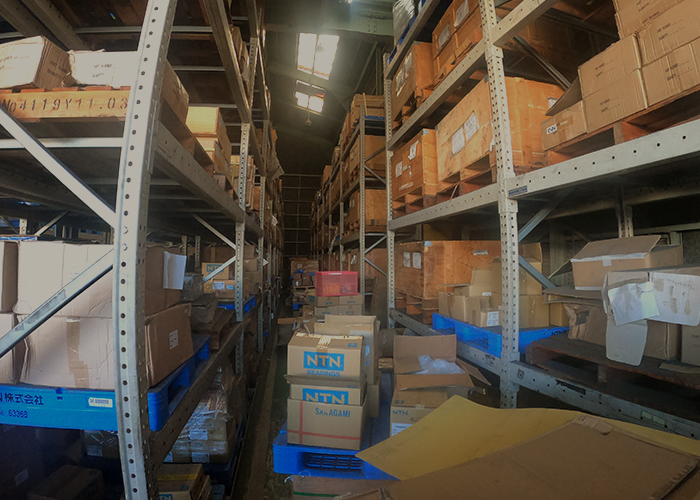
さらに、倉庫内では5S(整理・整頓・清掃・清潔・躾)が徹底されておらず、「床に商品が置かれる」「仮置きスペースが乱雑に使われる」など整理整頓が行き届かない状況が目立ちました。本来、スムーズな物流を支える基盤であるべき倉庫は、むしろ混乱の象徴と化し、現場は解決の糸口さえ見えない状態に追い込まれていました。
このような状況は現場スタッフに大きな負担を与え、熟練スタッフでさえ“たった1個”の商品を探し出すのに5時間以上かかるケースも発生していました。
整理整頓の行き届いていない倉庫内を探し回る心理的ストレスは作業効率を大幅に低下させるだけでなく、「次の商品も見つからなかったらどうしよう」という焦燥感がスタッフの集中力を奪い、通常のピッキングスピードを大きく損なう原因となっていました。
最終的に、商品が見つからなければ再入荷となるため余分なコストが発生することに加え、出荷スケジュールが遅延する事態に直面します。精密部品や産業用機器を扱う当社においては、迅速な納品が競合との差別化の要であり、このような遅延が顧客離れにつながるリスクは看過できませんでした。
【課題1の解決】ピッキングスピードは従来の3倍へ
あるはずの商品を探し回ることから完全に解放された
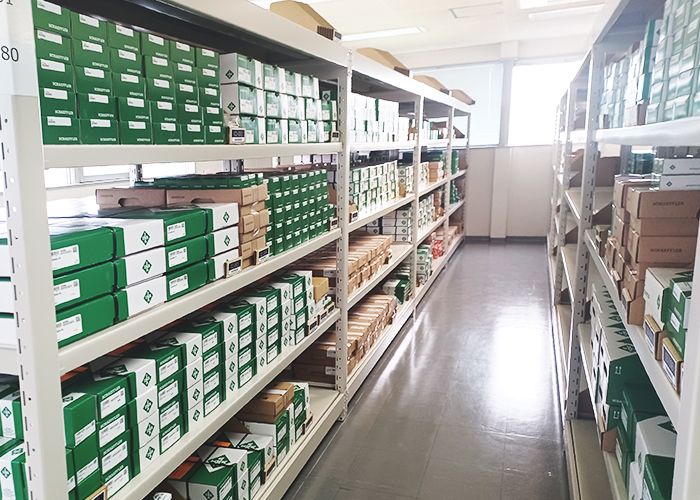
WMS導入によって正確なロケーションデータを誰でもリアルタイムで確認できるようになり、ピッキングスピードが従来の3倍以上に向上したことで、業務全体のスピードが劇的に改善されました。
この結果、人件費の削減につながったことに加え、責任者が物流フローの見直しや業務改善といった、本来注力すべき物流業務に専念できるようになり、現場全体のパフォーマンスが底上げされました。
また、倉庫管理システム(WMS)を用いたロケーション管理の徹底により、「商品を探す」という非効率な業務は一掃されました。従来は、商品が見つからない場合、「こういう時はこの辺りにある」という熟練スタッフの勘や経験に頼らざるを得ず、責任者クラスがその対応に多くの時間を奪われていました。
スタッフからは、「所定の場所に商品が無いかもしれないという不安が解消されて嬉しい」「作業がスムーズになり、気持ちに余裕が生まれた」といった喜びの声が多く寄せられています。これにより職場全体の雰囲気が明るくなり、チーム全体のモチベーションも大きく向上しています。
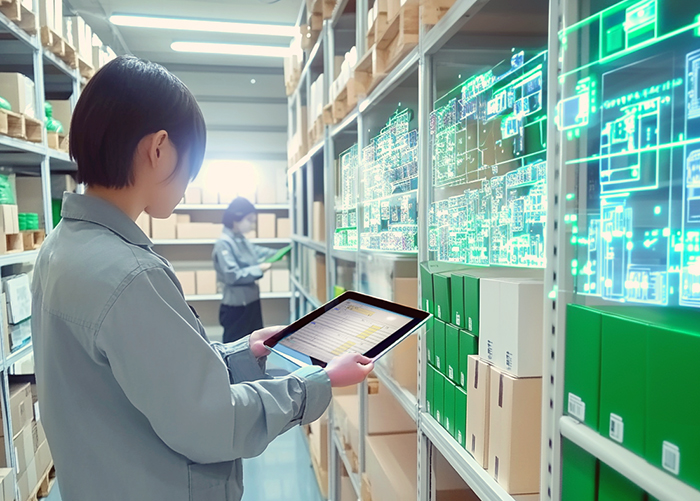
さらに、「在庫管理の見える化」によって、現場と営業部門の連携がかつてないほどスムーズになりました。従来は、営業担当者が現場に電話で在庫状況を確認し、その都度やり取りに時間を消費することが常態化していました。
三協さんの仕組みを導入してからは、リアルタイムで正確な在庫データを営業部門が簡単に把握できるようになり、商談の質が大きく向上しました。在庫状況や納品スケジュールに関する顧客の質問や要望に即座に対応できるようになり、その場で具体的な提案や納期の提示が可能となったことで、商談のスピードが飛躍的に向上し、成約率も向上しています。
【課題2】蓋の空いた70箱の試練:果てなき正解探し
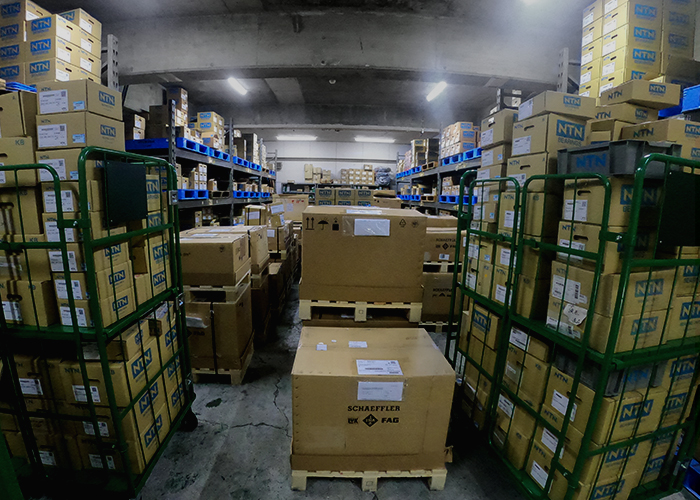
当社では、毎日15時までのご注文を当日中に発送しており、その数は1日で少なくとも70社以上に及びます。すべて企業向けの注文であり、1日に同じ企業から複数回に分けて注文が入ることが日常茶飯事です。
特に当社が扱うベアリングなどの精密部品は、特殊な機械を製造するメーカーからの注文が中心です。これらの企業では、「製造ラインのトラブル」「製品仕様の変更」「緊急の顧客対応」などが少なくありません。
そのため、決められた時間での注文に加えて、融通の利く「追加同梱」の対応が不可欠であり、これに柔軟に応える体制が求められます。
しかし、注文ごとに1件ずつ梱包すると個口数が増えるため、配送コストが膨れ上がってしまいます。そのため、当社では配送コストを削減するため、15時まで追加注文が入る可能性を見越して、各企業向けの段ボールをそのまま“開けた状態”で倉庫内に並べて追加注文分をその中に追加していくという運用を採用していました。
作業者は、蓋の開いた70箱以上もの段ボールから、該当する出荷先の箱を目視で探し出し、商品を間違えないよう慎重に詰めていく必要があります。しかし、その現場は、よく似た大量の段ボールが“ところ狭し”と地面に並べられた混沌の空間。各箱の中身はもちろん、出荷先も異なるため、スタッフは目を凝らし、集中力を最大限に発揮しながら正確さを保たなければなりません。
想像してください――無秩序に並んでいる70箱以上の蓋が開いた段ボールの間を、数十キロ以上の重いベアリング商品を抱えながら、たった一つの正解を探し出すプレッシャーは相当のものです。
しかも現場スタッフは50代以上も多く、腰を屈める作業を何度も繰り返すうちに、身体は疲弊し、精神的にも限界に近い負担を強いられる状況に陥っていました。
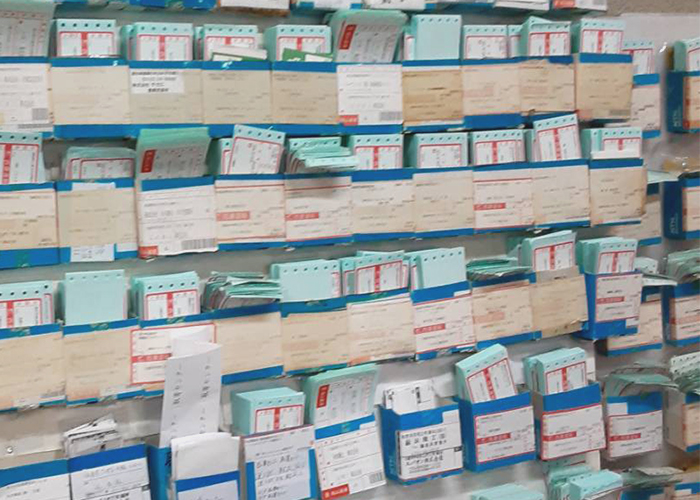
さらに、集荷時間の制約も現場にさらなる追い打ちをかけていました。運送業者の待機時間は短縮されており、以前のようにドライバーに待ってもらうということも難しい環境です。加えて、当社では3つの物流拠点から商品を集約して出荷していますが、別拠点から横持ちされた商品を正確に照合する作業も、集荷時間までに完了させなければなりませんでした。
このようなタイトなスケジュールの中で、アナログ対応を続ける限り、どれほど注意を払ってもミスが避けられない状況でした。送り状を誤って貼付したり、別の企業向けの商品を誤って同梱してしまうといったミスも発生しており、顧客から厳しい叱責を受けることもありました。
【課題2の解決】 追加同梱において、知識・経験は不要に
ミスしたくてもミスできない仕組み
三協さんに構築いただいた倉庫管理システム(WMS)の「同梱システム」は、「70個以上の蓋の開いた段ボールの中から正解を目視で探し出す」という追加同梱についても非常に大きな効果をもたらしました。
まず、最初の注文分のピッキングが完了した時点で、出荷先ごとに段ボールを置くべきロケーションがデジタルで自動的に紐づけられます。その後、追加注文が発生しても、紐づけられたロケーションに商品を同梱するだけで対応可能となり、ピッキングリストを見ればどの段ボールに商品を入れるべきか一目で分かる仕組みが構築されています。
その結果、納品先や商品の知識や経験がなくても同梱作業がスムーズに進むようになり、数十キロ以上の重いベアリング商品を抱えながら段ボールを探し回る無駄な作業は完全に解消されました。
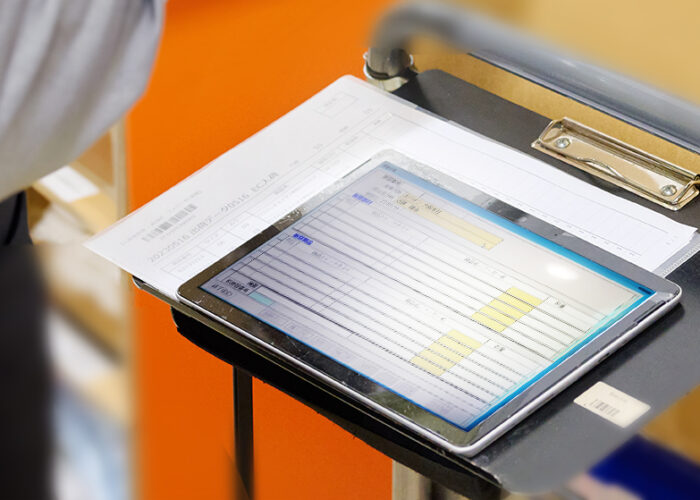
また、デジタル検品機能を導入したことで、ロケーションナンバー、納品書ナンバー、商品ナンバー、送り状ナンバーがすべて紐づけられ、手作業での確認が不要となりました。
「商品の入れ間違い」「送り状の貼り間違い」といったヒューマンエラーに加え、他の物流拠点からの横持ちでの突き合わせ作業においてもミスが無くなり、いわば「ミスをしたくてもミスできない」仕組みが実現できています。
また、この「同梱システム」の優れた特徴の一つに柔軟性があります。当社では、長さ2mmのミニチュアベアリングから2メートル以上の大型ベアリングまで、多様な形状やサイズの在庫を扱っているため、同梱するための保管スペースを事前に予測することは極めて困難です。
三協さんの同梱システムは、ロケーションを後から動的に拡張できる仕組みを備えています。
例えば、出荷先Xをロケーション①、出荷先Yをロケーション②、出荷先Zをロケーション③に割り当てたとします。その後に出荷先Xから大きな商材が追加注文された場合、従来はロケーション①のスペースが不足したらロケーション②やロケーション③のスペースを圧縮することによって、ロケーション①のスペースを確保していました。しかし、この方法では、アイテムが多い場合に玉突きのようにモノを移動させる必要があり、非常に手間がかかっていました。
この「同梱システム」は、その時空いている場所をロケーション①の拡張スペースとして動的に利用できる仕組みを備えています。すなわちはじめに割り当てたロケーションを気にする必要なく、後から追加されるサイズの大きなアイテムもスムーズに同梱作業を継続できるようになっています。この「可変的なロケーション構築」により、余剰スペースを有効利用しながら、追加同梱をミスなくスムーズに進めることが可能になりました。
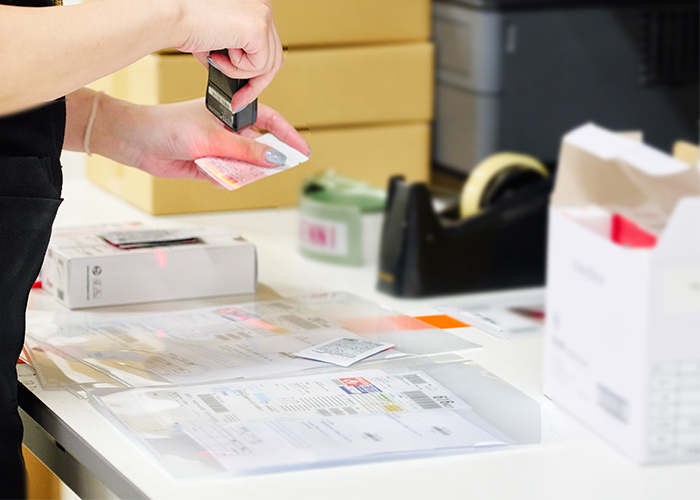
40~50代を中心とする作業者の負担が軽減されたのは本当に嬉しいです。これまで毎日おこなっていた「段ボールを探す」といったストレスの大きい業務は完全に解消され、現場の作業効率は格段に向上しました。その結果、スタッフは肉体的・精神的な負担から解放され、安心して作業に専念できるだけでなく、より快適で生産性の高い職場環境が実現しています。
さらに、「出荷ミス」「送り状の貼付ミス」「出荷遅延」といった物流品質が大幅に改善され、顧客からの評判も上々です。三協さんの物流改善により、現場の効率性と正確性は新たな水準へと引き上げられ、スタッフにとっても負担が少なく、働きやすい環境が整いました。
【課題3】修理不能のリフトが突きつける倉庫運用の現実
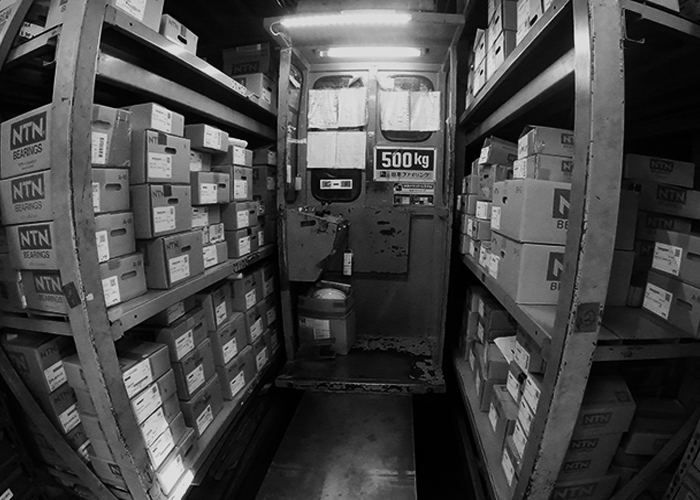
当社の倉庫には修繕が必要な設備がいくつかありましたが、その中でも特に目立っていたのが、狭い通路で上階へ荷物を運ぶための古びたリフトです。このリフトは、導入当初は画期的なマテハン(マテリアルハンドリング)機器として活躍していましたが、老朽化が進んだ現在では、動作時の軋む音が現場に不安をもたらす存在となっていました。
何十年にもわたり使い続けられてきたこのリフトは、修理がほぼ不可能な状態に陥っていました。必要なパーツはすでに生産中止となり、専門業者ですら修理を引き受けたがらない状況でした。
このリフトは製造から約50年が経過しており、当時の基準で設計された特殊な技術が使われています。万が一、リフトが故障して停止すれば、上階へのアクセスができなくなり、商品の運び出しが困難になります。結果として、倉庫全体の入出荷作業が滞る可能性があり、日々の注文対応に大きな影響を及ぼしかねない状態でした。
リフトの存在は、スタッフの働き方にも深刻な影響を及ぼしていました。突然止まるかもしれない老朽化した設備を使って高所作業をしなければならない現場では、常にリスクを抱えながら作業が進められていました。スタッフは故障の危険と隣り合わせで働き続ける中、身体的にも精神的にも大きな負担を感じていました。
この古いリフトは、当社の倉庫運用が抱える限界や課題をまさに象徴する存在となっていたと思います。
【課題3の解決】 マテハン選定の基準は、“流行り”ではなく “効果的に使い倒せるか”
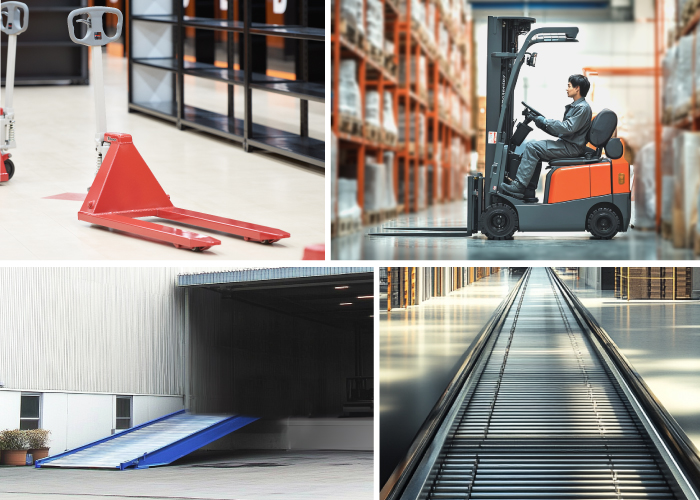
三協さんで入出荷頻度やロケーション効率を細かく分析していただき、老朽化したリフトの代わりに、リーチリフトやコンテナスロープといった代替設備が導入されました。
その結果、狭い通路や上層フロアへのアクセスが従来よりもスムーズに行えるようになり、現場の安全性と作業効率は飛躍的に向上しました。リフトに依存していた高所での不安定な作業が解消され、スタッフは故障リスクを気にすることなく、高所作業にも集中できるようになりました。
マテハンの入れ替えを進める際、当初は「物流ロボットや高額なマテハン機器の導入を提案され、必要以上の投資を求められるのではないか」と懸念していました。
しかし、三協さんからの提案は、ハンドリフト、リーチリフト、コンテナスロープといった、私たちの取り扱う商材や現場の物流フローを十分に考慮した実効性の高い内容に絞られていました。
AGVやピッキングロボットなどの高額な設備を“導入ありき”の姿勢で提案することは一切なく、“効果的に使い倒す”ことだけを前提としたマテハン選定がものすごく印象的でした。
こうした地に足のついた提案は、現場の細かな運用まで理解していない一般的な物流コンサルタントには実現が難しいものであり、「誤出荷ゼロ」を追求し続けてきた物流企業だからこそ可能な提案だと実感しました。三協さんのおかげで、必要最小限のコストで効率的かつ機能的な物流センターを構築することができたと感じています。
12,000枚のロケーション看板を自分で作る「物流コンサルタント」は日本中を探してもいない
物流改善の一環として大阪市内に新しい物流センターへの移管を計画していましたが、旧倉庫での入出荷業務が多忙を極め、新倉庫の立ち上げに協力できる余力はほとんどありませんでした。そんな状況の中、三協さんには新倉庫に何度も足を運び、提案やアドバイスにとどまることなく、実際に手を動かしながら立ち上げを全面的に支援していただきました。
精密部品という当社が扱う商品の特性を勘案した「ロケーション設定」や「業務フローの構築」にとどまらず、実際に使用するロケーション看板やラベルシールの作成、導入する保管什器の設置立ち合い、さらには旧物流拠点からの荷物の移し替え作業まで、先陣をきって進めていただいた姿勢には感銘を受けました。
特に心を動かされたのは、三協のコンサルタントさん2人が朝から晩まで一心不乱に地道な作業に取り組む姿です。彼らは専用の印刷機を使ってロケーション看板やラベルシールを印刷し、ラミネート加工を施したうえで慎重に1枚1枚貼り付けていました。
1階から4階まででロケーションが12,000か所あったため、二人で終わらせるには膨大な時間が必要だったと思います。本来なら高度な物流ノウハウが必要な工程ではないため、私たち自身でやるべきであり、三協さんは提案や監修に留まるところですが、私たちが忙しい状況を考慮してすべての作業を最後まで代わりにやっていただきました。
多くのコンサルティング会社が戦略構築を主業務とする中、たとえ実行支援を行う企業であっても、ここまで個別具体的に作業に取り組んでくれるとは想像していませんでした。そのため、三協さんの献身的な姿勢には深い信頼と感謝の念を抱かずにはいられません。
彼らの誠実な働きぶりとプロフェッショナリズム、そして人間味あふれる対応は、私たちに大きな刺激を与え、「ここまでしていただいている以上、物流改善を必ず成功させる」という強い決意を抱かせるものでした。
一刻を争う旧倉庫からの撤退戦
年単位で“800万円”の追加コストを削減
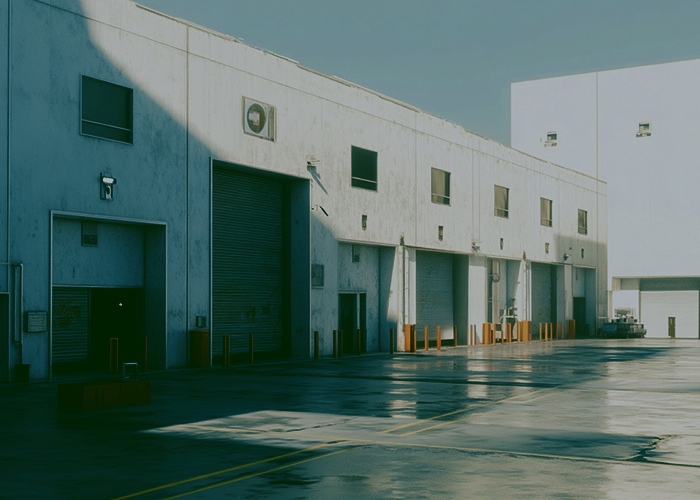
古い倉庫から新倉庫へ商品を移し替えるというのも、スピーディに進めなければならない理由がありました。その最大の理由は、旧倉庫が賃貸物件であり、毎月の家賃を勘案すると年間で約800万円ものコストがかかっていたことです。
しかしながら、当社はお客様の製造工程で不可欠な精密部品や産業用機器を扱っており、通常の入出荷作業を止めるわけにはいきません。したがって当面の期間は古い倉庫もそのまま使用するしかないという状況であり、新倉庫を借りた後も具体的に旧倉庫をいつまでに返すという算段も全くついていませんでした。
ところが、三協さんは「旧倉庫の返却が遅れれば、年間で約800万円の追加コストが発生する」と緊急性を指摘。驚くべきスピードで旧倉庫から新倉庫への荷物の移し替えに対応してくれました。移管スケジュールの構築、10トン車の手配、そして実際の商品仕分けから移し替え作業までを“たった5日間”で完了させてしまったのは驚きでした。
この迅速な移し替えが成功した要因は2つあったと思います。
まず1つ目は、引っ越しスケジュールの綿密な計画と、その計画を現場で実際に自ら実行する三協さんのリーダーシップでした。当社のための物流改善なので協力するのが当たり前なのですが、年長者も多いですし、やはり上から目線で正論を言われても物流現場は動かないものです。
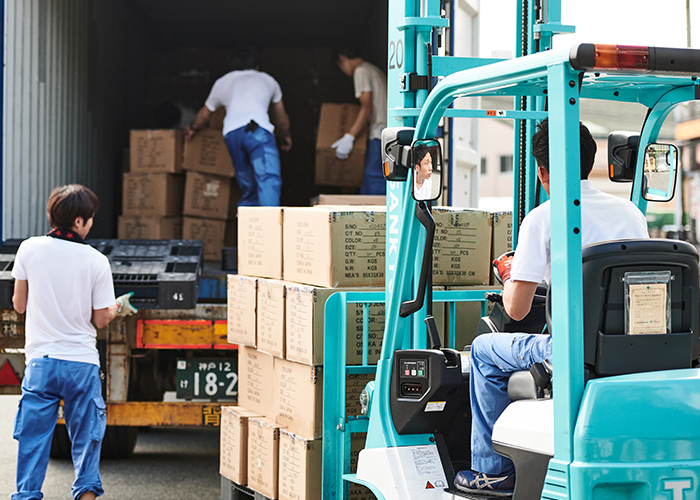
単に指示を出すだけではなく、自らがフォークリフトに乗り、現場の最前線で見本を示しながら荷受け作業をガンガン進める姿勢が、チーム全体の信頼と統率を生み出しました。
一般的な物流コンサルとは違って、率先して動く三協さんの行動を目の当たりにすることで、「当事者である我々が手を抜くわけにはいかない」という思いが自然と湧き上がることで現場の一体感が高まり、驚くほどスムーズな引っ越しが実現しました。
2つ目は、三協さんに構築いただいた倉庫管理システム(WMS)の「入庫システム」の存在です。当社ではアナログ管理が主流であり、データ上の在庫と実際の在庫に大きな乖離がありました。また、ロケーション管理の不徹底により、元データをそのまま信用できる状況ではなく、引っ越しの際には全商品をスキャンして入荷情報を正確に記録する必要がありました。
しかし、実際には全アイテムの約10%でバーコードシールが貼られていない状態であり、「どの商品にバーコードが貼られていないのか」という情報もありませんでした。さらに、バーコードが貼られている商品の約60%において、「バーコードは貼られているものの、商品マスタにそのバーコードが登録されていない」状態だったのです。
このため、入庫時のバーコードスキャンで頻繁にエラーが発生することが想定され、結果として入庫作業には相当な時間を要することが懸念されていました。
こうした課題に対し、三協さんの「入庫システム」には当社の実態に合わせた柔軟なカスタマイズが施されていました。市販のパッケージ型WMSであれば、商品マスタに登録されていないアイテムがあるたびにエラーが発生し、入庫作業が中断されるでしょう。
三協さんのWMSでは、バーコードが貼られていない商品の場合、外箱に記載された品番を入力するだけでその場で自動採番されたバーコードシールを印字できます。
この仕組みは、品番と採番されたバーコードを事前にマスタデータで紐づけるプログラム処理によって構築されており、作業効率の向上とデータ管理の正確性を両立させています。
もしも三協さんの「強力なリーダーシップ」と柔軟な「入庫システム」がなければ、移管作業は大幅に遅延し、家賃負担がさらに膨らむことは避けられなかったでしょう。旧倉庫を想定よりもずっと短期間で返却することができたため、年間800万円弱というコストを削減することができました。
物流改善で明らかに変わった“スタッフの意識”
品質や生産性が改善したことは、これまでお話ししてきた通りですが、それ以上に大きく変わったのは、スタッフの意識ではないかと思います。物流現場で働くスタッフから、これまでにはなかった前向きな提案が次々と生まれるようになりました。
たとえば、「ピッキングリストに伝票番号の始まりと終わりの番号を表示させる機能を追加したい」「ロケーションマスタを新しく登録して、自分たちの考える棚割でロケーションを試してみたい」といった具体的なアイデアが物流スタッフから頻繁に飛び出すようになりました。
また、これまで締め時間を過ぎた追加同梱については、やむを得ず個口を増やして対応していましたが、「締め時間を過ぎても個口を増やさずに同梱が出来る仕組みをデジタルで構築しよう」といった、コスト意識や顧客視点を持った発想も生まれています。
こうした積極的な取り組みや提案が、スタッフから自然に出てくるようになったのは、まさに意識改革の結果だと思います。この意識変化をさらに後押ししてくれたのが、三協さんの存在です。スタッフから出た新しいアイデアに対して、三協さんは頻繁に“壁打ち”の相手になってくれています。スタッフの考えや提案に耳を傾け、具体的なアドバイスやフィードバックを提供してくれることで、アイデアがより洗練され、実現可能な形に進化しています。
「この仕組みをこう改良したらどうなるのか?」という問いに対して、三協さんは「試すことで得られる結果」や「実際の運用における注意点」を具体的に示してくれるため、私たちにとってはある種の“答え合わせ”をしてもらえるような感覚です。
このようなアフターフォローのおかげで、スタッフの提案が形となり、現場全体の改善が継続的に進んでいます。
スタッフがただ与えられた業務をこなすだけではなく、自ら改善点を見つけ、積極的に提案し、現場をより良くしていこうという姿勢を持つようになったことは、物流運用全体にとって大きな変革です。
この変化は、単なる業務改善に留まらず、私たちの物流センターの未来を切り開く原動力となっています。そして、この意識変化を育むために、常に寄り添い、壁打ちの相手として支えてくれる三協さんには、感謝の気持ちでいっぱいです。これからも三協さんとともに、新しい改善のサイクルを続け、より高い品質と生産性を追求していきたいと考えています。
企業情報
- 事業概要
- 軸受けおよび付属品の販売
- 取扱いアイテム数
- 約26000SKU
エバオン株式会社
創業80年以上と歴史ある軸受(ベアリング)を扱うメーカー。海外にも拠点を置き、グローバルに事業を展開している。 ベアリングにとどまらず産業ロボットや医療分野等の特殊用途製品なども扱う。